The teams began by determining if the sign could be moved and affixed to a newly installed concrete foundation; however, this idea was quickly dismissed, as the sign would fall outside the property line.
TDH then considered converting the original pylon design to a projecting sign. While this seemed to be the most logical option, it required the welding of steel support arms to the building’s steel structure, which was nearing completion. To efficiently accomplish this addition, the crew escalated the approval of the sign placement, which allowed enough time for the steel supports to be engineered and installed without affecting the building schedule.
Recreation through fabrication
Once all approvals were in place, TDH’s fabricators began stripping and cutting out the sign’s rusted components. The installation’s old electrical wiring was also removed and its fluorescent tubes and ballasts were replaced with light-emitting diodes (LEDs).
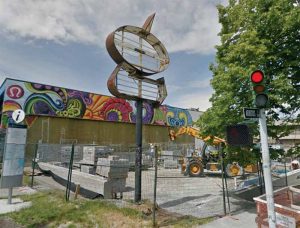
Due to complications surrounding the existing concrete pad, TDH opted to convert the original pylon design to a projecting sign.
The majority of the structure was rebuilt with 6.4- x 51-mm (0.25- x 2-in.) welded angle and then sheeted to provide a clean finish. Extra attention was taken in securing the ‘yogo’—the brand’s signature logo shape—to the sign’s vertical pole, as this aspect needed to be as discreet, but also strong enough to support the top of the sign.
Transport was also a consideration, as the installation’s size made this process very costly and difficult to achieve with the sign in one piece. Thus, the lower ‘arrow’ portion was built separately with an internal attachment plate to secure it to the upper ‘oval’ portion. This allowed the sign to be transported from the shop to the site on one truck bed. The two pieces were then hoisted by crane and assembled on-site before being lifted into place.
The engineered attachment design allowed the sign’s steel tube arms to slip inside the steel structural tubes that had been welded to the building’s steel structure. The tolerance, however, was only 6.4 mm (0.25 in.), which meant the welding to the building steel needed to be accurate, as did the tube placement on the two sections of the sign.
As the sign was comprised of two separate pieces, it was necessary to determine precisely how these sections would fit together prior to installation. As such, TDH completed three site inspections to ensure the tube arms of the sign they were fabricating aligned with those fixed on the building.
A seamless installation
To complete the installation, TDH partnered with fellow Vancouver-based sign shop Tops Lighting, which provided the large equipment required for the job, as well as qualified personnel with many years of experience.