By Bill Dundas
Sign installation work requires the proper training, equipment and procedures. When followed and used correctly, these factors combine to create a safe and efficient work environment.
Some of the key safety precautions for sign installers may seem obvious at first glance, yet these are exactly the requirements that are needed to prevent the most common types of occupational accidents and employer liability. So, even well-known safety rules are not always put in practice.
On-the-job training is certainly valuable, but formal safety training is truly essential. Without formal training, sign installers who have learned strictly by watching others at work are often left unaware of certain crucial safety requirements. And since the work they perform encompasses a variety of trades, it is essential for them to have broad-based training.
Proper equipment
The heights involved in sign installation work make fall-protection equipment essential. Occupational safety rules call for the use of personal protective equipment (PPE) in a variety of forms.
Safety harnesses, which are designed to prevent injury in the event of a fall, are a key requirement in terms of PPE. Each worker should have his/her own harness, properly adjusted for individual use. Although employers provide this equipment, each worker is responsible for maintaining it in good condition and reporting whenever a safety harness is damaged and needs to be taken out of use.
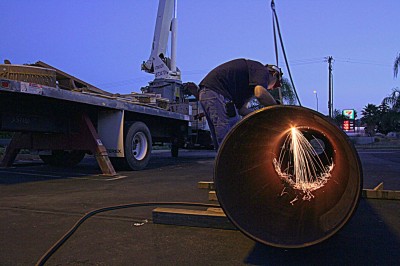
Welding masks incorporate special dark-tinted lenses to prevent the eyes from being injured through exposure to arcs.
Other types of PPE required by occupational safety regulations include goggles and face masks, which are important safety gear for sign installations that involve torch-based cutting, welding, drilling and hammering. Welding masks incorporate special dark-tinted lenses to prevent serious eye injury, which could otherwise be caused by exposure to welding arcs.
As sign installation work entails overhead hazards, hard hats should always be worn on the job by sign installers. When one installer is working in an aerial bucket and another is standing on the ground below, for example, there is a potential hazard in the event that tools or other items are accidentally dropped from above.
It is also important to wear ear protection when operating noisy power tools, such as rotary hammers, concrete saws, circular saws and pavement breakers. Otherwise, a sign installer’s hearing can be damaged by noise levels above a safe level.
Just as seatbelts have been shown to reduce the number of automobile injuries and fatalities, so too does PPE make on-the-job accidents less likely for sign installers.
Electricity and cranes
Overhead electrical power lines represent one of the most serious hazards for sign installers. In fact, the top cause of fatalities for workers who use cranes is when the equipment accidentally comes into contact with a power line.
The following are some examples of occupational safety rules to be followed when installers are working in proximity to these lines.
- Confirm with the power company the line has been de-energized and is visibly grounded at the work site.
- Ensure no crane, load line or load hoisted by the crane comes within 6 m (20 ft) of the power line.
- Follow clearances based on the power line’s voltage. For example, 50-kV lines require a minimum clearance distance of 3 m (10 ft), while those exceeding 250 kV require a minimum clearance of 6 m (20 ft).
An additional option occasionally used by sign installers is known as ‘booting.’ This method involves contacting the power company to dispatch a service crew to cover the lines with special insulating sleeves or ‘boots.’ While it represents an extra safety precaution, however, it does not relieve sign installers of their responsibility to observe one of the three options above.