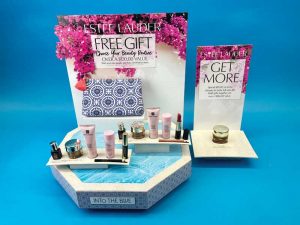
L&A Diecrafts Ltd. works with their partnering companies to produce a variety of paper and cardboard displays. Images courtesy L&A Diecrafts
By Megan Beach
For more than 50 years, L&A Diecrafts Ltd. has strived to deliver striking, high-quality projects. Based out of a manufacturing facility in Burlington, Ont., the company specializes in large-format die cutting, mounting, D-taping, assembly, and packing. They also work in conjunction with their partnering companies, R. Jones Print and Display Inc. and Cool Display Solutions Inc., to produce a variety of paper and cardboard displays for the commercial market.
Throughout their daily practices, L&A demonstrates their commitments to pushing boundaries and embracing cutting-edge technology. This has resulted in the integration of two high-speed, hot/cold-melt computer numerical control (CNC) glue tables, to help their team streamline production for both assembly and packaging of their display projects.
Simplifying glue distribution
Each machine features a touch display with programmable buttons, where the operator can choose where they would like to start and stop each desired glue pattern on the layout, as well as draw it using a joystick and a laser. When they are looking at the screen, they can see where the camera and laser are pointing, but will also be physically close enough to see it in front of them on the machine. Possible patterns consist of straight lines, dots, swirls, and arcs, which can be extended, shortened, or made wider. Once the program has been set in the system, it can be saved for future use, in case a project needs to be repeated.
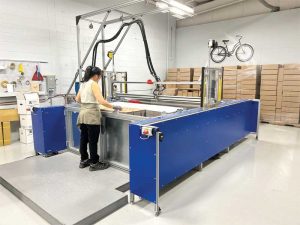
Integrating two highspeed, hot/cold-melt computer numerical control (CNC) glue tables has helped their team streamline production for assembly and packaging of their projects.
After setting the pattern, the operator can choose the consistency of the glue, as well as the temperature setting, which can be either hot melt, slow-set hot melt, or cold melt. Typical hot melt will begin to skim over when it starts to cool, which may not be ideal for assemblies that take a bit longer, as the glue might already be setting and will not stick. However, slow-set hot melt has a larger, longer open time, which helps it stay tacky. By comparison, cold-melt glue has a similar consistency to white glue, but it is usually more messy to apply and takes longer to cure, as it is a wet glue. Ultimately, slow-set hot melt is the most effective setting for paperboard displays, as it cures quickly to ensure the glue will stick properly the first time, without the need for any extra weight.
With their program and gluing settings selected, the operator can press down on the start/stop pedal to begin distributing the glue. This can be controlled manually or placed on a timer, to allow for assembly and reloading once each piece is finished. There is also an option to turn one of the four stations on or off independently if an employee needs to walk away or refill the machine.
Elevating efficiency and precision
CNC glue tables allow for consistency in glue application, aligning with L&A’s commitment to delivering meticulously crafted, quality products, and seamlessly integrating into their comprehensive suite of services. From large-format die cutting to intricate assembly and packing, this technology complements the company’s existing processes, amplifying capabilities across the production line.
Using the machines ensures the same amount of glue will be placed in the same spot for each unit of the display. It also guarantees this is done quickly and accurately, with minimal interruption. Previously, these areas would have been D-taped in the desired locations before the sheets were die cut. Then, once the piece was ready, the team would need to pick off each individual liner to case wrap the box. The glue tables eliminate the need for this step, as well as ensure the next piece can be glued while the current one is being assembled.