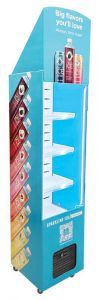
L&A also has the ability to make larger displays, including wrapped cardboard refrigerators for supermarkets, liquor stores, and restaurants.
Enhancing productivity and turnaround
The automatic glue pattern application feature also significantly reduces production time. This enhancement translates to faster turnarounds without compromising the quality of the project. Further, the slow-set hot melt process allows for more forgiveness when sticking pieces together, whereas D-tape is stuck down as soon as it touches another surface and cannot be fixed. This setting allows the glue to be peeled back, finessed as needed, put back down, smoothed out, and handed off for assembly.
The ability to save project outlines also helps increase productivity, as it allows the team to recall a program if a similar project comes up later. Each machine can then be programmed to glue the same piece at all four stations—for a total of eight stations—or split to focus on a different piece at each location and pack the finished display off the machine.
Empowering project assembly teams and minimizing loading time
The ergonomic design of the machines removes strain from employees’ hands by eliminating the need to constantly hold the trigger of a glue gun during the application process. The tables dispense melted glue from tanks, or pots, which have the capacity to hold a large amount of glue pellets. Unlike a glue gun, where the stick needs to be replaced more frequently, each pot can be filled with pellets and stay full while working on a multitude of projects, which streamlines the process of using melted glue.
Further, the incorporation of two elevating tables minimizes machine loading time, which reduces downtime, increases focus, and maximizes operational efficiency. Each table can fit a large number of pieces to be glued, which eliminates the need for employees to continuously leave their stations to pick up more parts for preparation or assembly.
Strengthening the commitment to innovation
The addition of CNC glue tables to their production process exemplifies L&A’s commitment to innovation. This forward-thinking approach aims to set new industry benchmarks for efficiency, precision, and technological advancement in large-format display manufacturing.
These machines have helped the company streamline the construction process for a variety of projects. While they focus primarily on case wrapping, L&A also has the ability to make larger displays, including wrapped cardboard refrigerators for supermarkets, liquor stores, and restaurants.
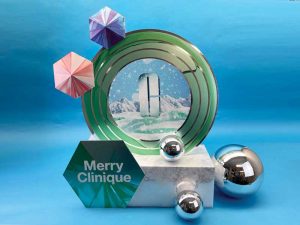
The majority of the company’s projects are within the short-run category, which usually reaches a maximum of 3,000 or 4,000 displays per project.
Using one table, the team can apply glue to the sides of the display, with three different glue patterns per side. Then, they can roll the sheet down a set of rollers to the next table to glue the back, transport it to the other side of the machine, and glue it all together. In total, five pieces can be glued in one fluid motion. This is an example of a project which would use the hot melt setting versus the slow-set hot melt, as it needs to cure instantly. The cardboard is also much heavier and would require more glue to hold.
The company also has the opportunity to do short-run packaging by request, another area in which the glue tables prove useful. In fact, the majority of L&A’s projects are within the short-run category, which usually reaches a maximum of 3,000 or 4,000 displays per project.
Megan Beach was brought up surrounded by friends and family in the die cutting and display industry. She first joined R. Jones Print and Display—the sister company to L&A Diecrafts Ltd.—18 years ago. Then, in 2017, Beach transitioned to take over L&A. With a meticulous attention to detail, she enjoys collaborating closely with colleagues across all departments to deepen her expertise.