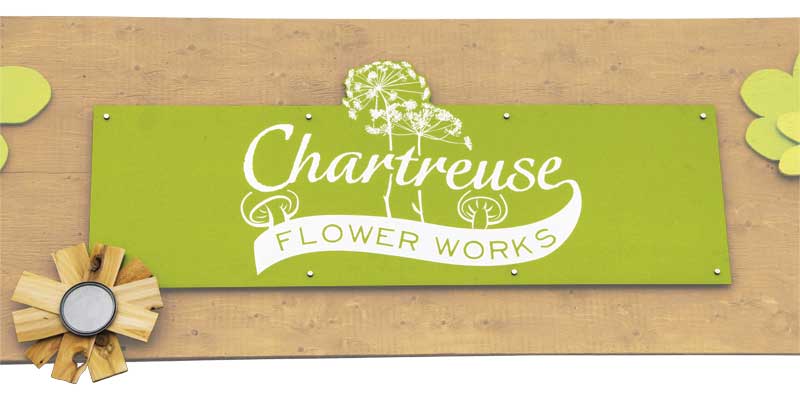
Sarah Toupin of Kingston, Ont., digitally printed this sign on 3-mm (118-mil) thick Dibond.
Photo courtesy Sarah Toupin
By Peter Saunders
Many popular substrates for the sign and graphics industry are not simply base materials, but rather ‘sandwiches’ that combine multiple layers of different materials to create new composites. Over time, these materials have continued to be customized for signmakers’ changing needs.
Stained glass via foamboard
By way of example, when artist Calley O’Neill of Waimea, Hawaii, designed a new 15.8-m (52-ft) long forest-inspired stained glass mosaic mural for Maui’s Pukalani Elementary School, she decided to experiment with a new process she had developed with fellow artist Lamar Yoakum, using a heavy-duty graphic display board.
Titled ‘Na Wao A’O Pi’liani’ (The Life Giving Forests Of Maui), the mural was commissioned by the Hawaii State Foundation on Culture and the Arts, as part of its Art in Public Places collection, for installation on an exterior wall of the school. Measuring 4.3 m (14 ft) tall at its peak, the mural would involve the work of nearly 260 Pukalani community members, including teachers and some 185 students from the school’s Grade 4 and 5 classes.
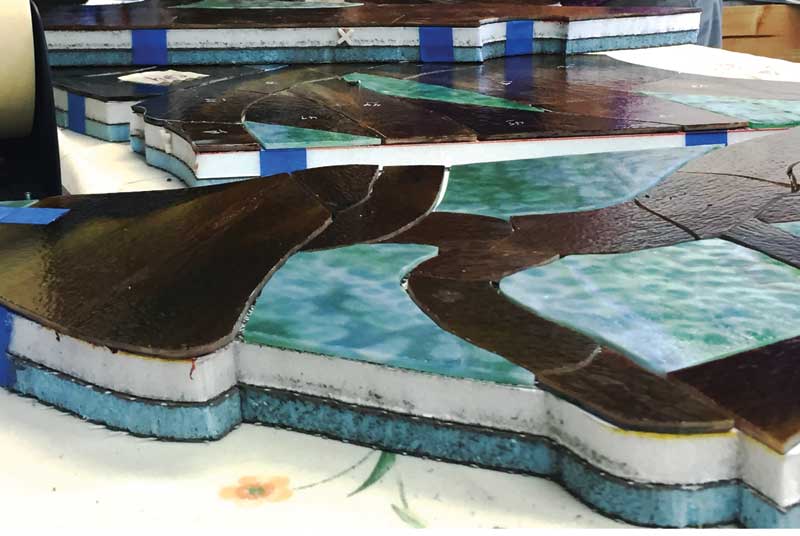
Gatorfoam boards recently supported the assembly and installation of a stained glass mural in Pukalani, Hawaii.
Photo courtesy 3A Composites
O’Neill and Yoakum turned to a composite material consisting of polystyrene (PS) foam bonded between two layers of a wood-fibre veneer laminate, both to create a detailed mosaic pattern and to work on with the glass pieces. Three full-sized cartoons of O’Neill’s master plan were printed. The first of these numbered clear pencil line drawings was preserved as a blueprint and base pattern, upon which to place the actual mural each time it was fitted to a floor. The second was adhered to 12.7-mm (0.5-in.) thick white panels of the graphic display board and jigsaw-cut into a puzzle of 75 segments, which were sandwiched with light cement-based building panels and complemented with an additional 95 graphic board segments for the border. Finally, the third—printed on thin polyester sheets—was hand-cut with pattern shears into 3,350 pieces to guide the glass cutting, leaving 3.2-mm (0.13-in.) spaces between the pieces.
“This way, we were able to create the design and check it on the school’s gym floor twice before installation,” O’Neill explains. “While the 3,350 completed stained glass pieces on the cement building panels were heavy, we were able to construct the design on the foamboard panels, which are very light, rigid and water-resistant, so we could easily carry these pieces around our shop and to the wall. We’re very happy with the results and the technique we developed.”
After the stained glass pieces were shipped from O’Neill’s studio by truck and barge to the school, they were covered with mosaic tape, lifted and installed into thin-set mortar on the wall. The installation was completed in one week by a four-person team, directed by Isaac Homza of Higher Standard Tile and Stone.