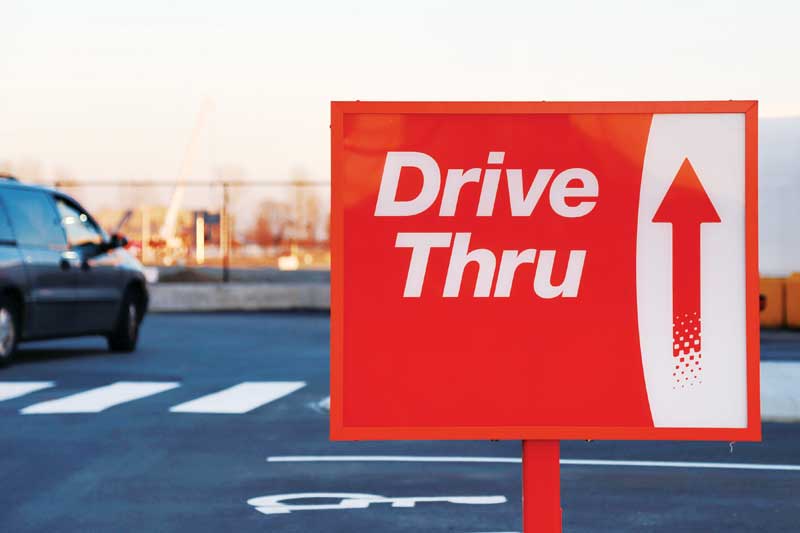
Many shops now use aluminum composite materials (ACMs) when fabricating sign cabinets.
Photo courtesy Piedmont Plastics
A process of evolution
Specifically, the school mural used Gatorfoam boards from 3A Composites, which also manufactures Dibond aluminum composite materials (ACMs), Fome-Cor clay-coated paper-faced foamboards, Sintra polyvinyl chloride (PVC) boards and Smart-X recyclable foamboards, which combine an expanded PS (EPS) core with two layers of high-impact PS (HIPS).
“We have batch processes that allow us to take dissimilar materials and sandwich them together,” explains Douglas A. Twitchell, 3A’s vice-president (VP) of marketing for the Americas. “We closely monitor product developments by wide-format printer manufacturers, so whenever new models become available, we’re ready with tried and tested materials that are compatible with them.”
When new inks are formulated, for example, it is important for substrates to be able to receive those inks effectively, which may call for a composite approach.
“You want a bright white substrate to ensure colours ‘pop,’ but it can be difficult to make the surface more ink-receptive while maintaining that white point,” says Twitchell. “Beyond the core material, it’s a question of which coatings you add to the surface. Some ultraviolet-resistant (UV-resistant) coatings, for instance, will add a yellow cast, reducing the whiteness of the surface. The goal is to provide the highest-quality printing surface possible.”
For the sign shop, meanwhile, the choice among various composite substrates will depend on the intended application and its environment. A foam core with paper faces may be appropriate for temporary indoor signs and point-of-purchase (POP) displays, while rigid boards with a wood-fibre veneer skin offer a wider variety of thicknesses and levels of durability.
The most durable options are ACMs. Brushed finishes are available for interior use, but their primary applications are outdoors, including larger monument signs that must cope with wind loads. Similar materials are even used for cladding buildings.
“We can mix and match substrate cores and surfaces both for the architectural market and for signs and displays,” Twitchell says. “It’s a process of evolution for existing technologies.”
By way of example, 3A is developing lighter foamboards with balsam plywood veneer panels, as well as custom colour-matched panels for more visually creative fabrication projects.
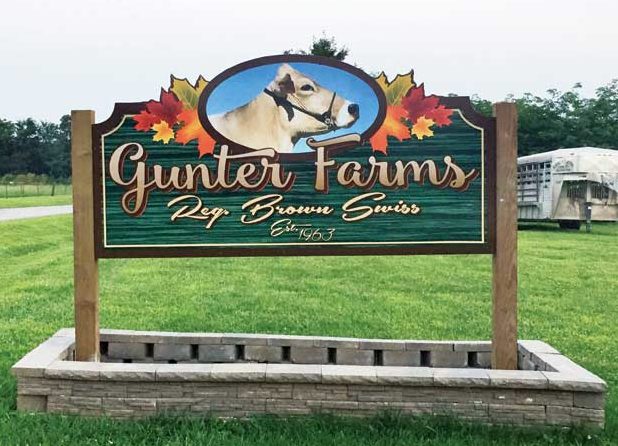
ACMs are replacing plywood in traditional-style signs because they offer greater weatherability.
Photo courtesy Grimco
The versatility of ACMs
There has also been a process of diversification specifically for ACMs, given their versatility across various industries.
“There can be very significant differences, depending on the type of skin on the product,” says Ted Isbell, a graphics specialist for Piedmont Plastics, which distributes sheet, rod, tube and film products across North America. “It can range anywhere from 0.08 to 0.5 mm (3 to 20 mil) in thickness.”
Piedmont’s most common option is a 0.2-mm (8-mil) skinned standard-grade ACM for flat sheet applications, but the company also recommends a 0.3-mm (12-mil) version for bending, three-dimensional (3-D) forming and V-grooving, as well as applications with wind loads.
“If you go as thin as 0.15 mm (6 mil), there will be durability issues, as the material will dent fairly easily and won’t stand up to a lot of abuse,” Isbell says. “There are also varying grades of aluminum. Some are harder than others. We test them in the field and gather customer feedback.”
As mentioned, one of the primary concerns for print service providers (PSPs) is ink adhesion. This has gotten much better, Isbell explains, with today’s flatbed printers processing ‘digital-grade’ matte-finish ACMs, which can support adhesion not only at the printing stage, but also through finishing, as the edges are engineered to prevent chipping during routing.