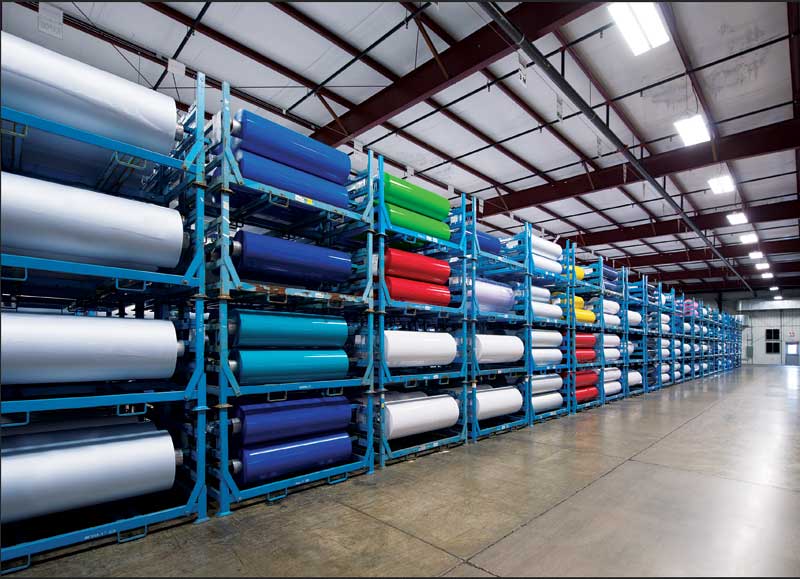
With greater uniformity throughout the manufacturing process, vinyl films can be consistently specified to tighter standards of thickness, colour, width and gloss level.
Plasticizer performance
While the difference between cast and calendered films is most frequently expressed in terms of their respective manufacturing processes, it is also a question of the particular ingredients added to the raw materials during manufacturing.
Most printable graphic films are made from the same basic raw material: polyvinyl chloride (PVC). In its unadulterated state, however, PVC is hard and inflexible. To provide the flexibility required for wraps and other graphic applications, a plasticizer must first be added to the PVC resin.
There are two primary types of plasticizer: monomeric and polymeric. The selection between the two will significantly affect the properties of the film.
Monomeric plasticizers consist of relatively simple, linear molecular chains, with a low molecular weight. They are considered the ‘economy-grade’ option, providing pliability for the film’s handling, but offering less durability than with polymeric plasticizers. Polymeric plasticizers are more complex, with a higher molecular weight, which leads to greater viscosity and better stability.
In the past, calendered vinyl was often associated with monomeric plasticizers, while only cast vinyl used polymeric plasticizers. Today, however, a new generation of calendered vinyl has been produced using polymeric plasticizers. As a result, the attributes and performance of calendered films have become closer to those of cast vinyl, including durability for several years, even though their manufacturing processes remain completely different.
Supporting sustainability
Another differentiator between vinyl films is their sustainability. Traditional plasticizers are now recognized to be less than environmentally friendly, so many raw film manufacturers have sought to use alternative ingredients, such as non-phthalate plasticizers, in the production process.
Used primarily to soften PVC, phthalates are easily released into the air and pose health problems when ingested, particularly by children. By offering phthalate-free films, manufacturers are proactively taking steps to meet customers’ needs with a commitment to sustainable development and responsibility toward the environment.
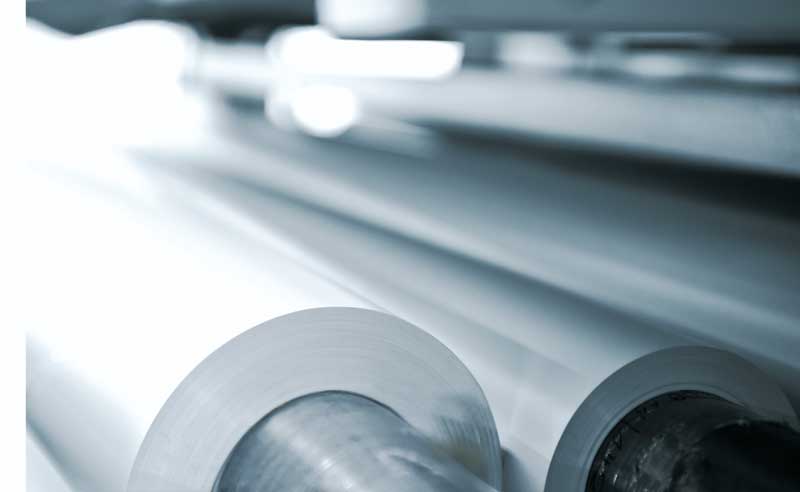
Calendered vinyl is produced in a continuous process, which enables high-volume, low-cost manufacturing.
Following years of research and development (R&D) and testing, phthalate-free films can now comply with industry regulations, such as Europe’s Regulation on Registration, Evaluation, Authorization and Restriction of Chemicals (REACH), while providing the same quality and reliability as existing phthalate-based films.
As with higher-quality calendered films using polymeric plasticizers, these new options are helping transform the market.
Consistency control
Manufacturing advancements over the last few years have also allowed vinyl, both cast and calendered, to be held to higher specification standards. Working together, software and hardware can hone in on microscopic features and control them from batch to batch, to help ensure a high level of uniformity.
Intelligent control systems measure and monitor a number of parameters relating to both the machinery and the materials as they are manufactured. Film properties like thickness, colour, width and gloss level, all of which are crucial to overall quality, are constantly controlled. With greater uniformity throughout the whole manufacturing process, the films can be specified to even tighter standards without sacrificing consistency.
Just as designers drive the creativity behind today’s striking and decorative wide-format graphics, so too do vinyl film manufacturers use knowledge of the latest science to turn technological innovations into reality.
Renaat Demeulemeester is president of American Renolit Corporation (ARC), which manufactures plastic films for car wraps and other graphic applications. For more information, visit www.renolit.com.