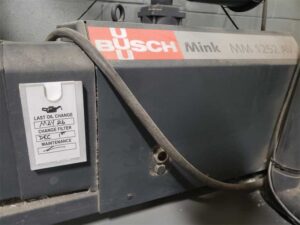
It is also important to keep maintenance logs with the equipment to see when the last check was made, or the last oil change occurred.
Outsourcing (printing, bending, fabrication, etc.)
Con: Expensive (less profit margin).
Con: Unpredictable timelines (at mercy of wholesaler).
Con: Quality control happens after the product is received in-house. If the wholesaler misses a quality check and it arrives at the sign shop ready to be installed, finding an issue at this point can be troublesome. Typically, the turnaround time to fix the issue(s) is not quick.
Pro: Less overhead costs (project management only).
Pro: The ability to reach out to more than one wholesaler to increase workload (although higher workloads does not necessarily mean higher profit margins).
With these pros and cons in mind, before one purchases or leases new equipment, they should draw up a comparative report from their previous three to five years without the equipment and forecast the next three to five years with the equipment. Also, one should ask themselves a few questions such as:
- Who will be operating the new machines?
- Will the sign shop need to hire more people to operate the equipment? (How much time will this take to learn/train?)
- What are the maintenance costs? (Can the equipment be fixed in-house or will one need to hire a technician to repair?)
- What does the upkeep involve? (e.g. oil changes, belt replacement, chains, blades, etc.)
- Does the sign shop have enough power to run this new equipment? (computer numerical control [CNC] machines and 3D printers, for example, can require high power demand)
- What other pieces of equipment will be required to operate the new purchase? (e.g. air compressors, pumps, filters, etc.)
- What safety-related issues will one run into? (What type of planning is necessary should something go wrong?)
- Does the shop have the space to accommodate the equipment? (Will valuable operating space be lost?)
- What is the depreciating value factor of the machine? (Can the equipment be resold without taking too much of a hit if it does not work out?)
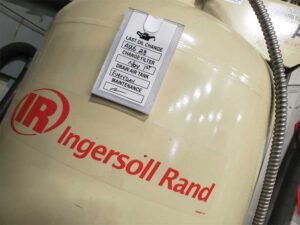
The person checking the equipment should sign their name in the maintenance log as it not only keeps them accountable, but also puts less strain on the shop owner knowing the equipment is being checked and the need for costly repairs are less likely.
After answering these questions, a sign shop owner should then prepare a cost analysis of what it would cost to hire someone to make a sign without having to purchase the equipment versus what it would cost to make the sign entirely in-house. The cost should then be multiplied by the shop’s forecasted sales (using the machines) to see how long it will take to pay them off.
This formula will differ from shop to shop as everyone likes to operate differently. That said, this author has found great success and control with owning their equipment—whether it be trucks, augers, tractors, trailers, printers, CNC machines, channel letter benders, paint booths, etc. By operating in this fashion, the author’s company has greater control over its product and takes pride in the fact a large percentage of the shop’s work is produced directly by their skilled staff and operating equipment.
Maintenance on equipment
As many in the sign industry are aware, equipment maintenance can be hard on the pocketbook. Some shops do not have the time to fix the equipment on their own, while others may be worried about their ability to repair it properly and if it is even safe for them to do so.
These are all great questions to ask; however, it is important to step back and think about the problem, how hard can it be to repair, and can someone on staff be trained to do this work? The answer is yes. This is a trainable skill. Keep in mind, the author is not talking about an engine rebuild or an electrical diagnosis but, rather, simple maintenance such as greasing fittings, changing the oil on trucks and equipment, checking and changing filters, inspecting leaks and tightening loose connections, and replacing cables and belts. The internet (YouTube in particular) is an extremely valuable resource for these types of repairs.