By Jason Remnant
There is no surprise the digital wide-format graphics market is advancing due to better printers, which are driven by higher performance and more flexible printheads. Across the whole range, higher driving frequencies deliver greater productivity at low costs.
Printhead performance is improving too, but this comes at a cost. Manufacturers spend a large share of their annual budget—often more than 10 per cent of sales—developing the next generation of printheads. This does not even include the millions of dollars required in investments to manufacturing capacity.
Newer devices offer high productivity with thousands of nozzles in one printhead. In addition, more than one colour per printhead makes integration and printer setup easier. For example, some printheads can offer four colours per unit. Also, newer devices offer much more flexibility and have the ability to jet more types of fluid including both solvent and aqueous inks. Not only does this fulfil the need for solvents in emerging global markets, but also allows the use of textile inks for soft-signage applications. They are also capable of jetting more viscous inks.
Where is the technology headed?
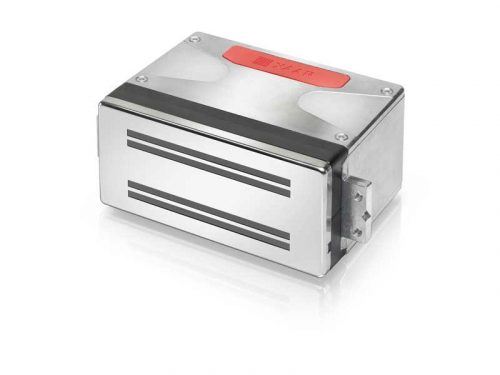
Some printheads can offer four colours per unit. Also, newer devices offer much more flexibility and have the ability to jet more types of fluid including both solvent and aqueous inks.
The holy grail for digital inkjet print has always been to economically deliver extremely fast printing with quality that, at the very least, matches traditional print methods. The transition toward speed—and the resultant productivity—along with the use of more aqueous inks are still the important drivers everywhere. This has resulted in an increased demand for greater productivity—higher production uptime as well as superior image quality. Most printers now provide and/or exceed the print quality needs required by most wide-format applications. They can print image quality in excess of 1200 dots per inch (dpi) at lower costs and higher productivity levels.
Also, greyscale printheads can print in varying conditions, such as different amounts of ink and printing modes. Eight-level greyscale allows raster image processors (RIPs) to achieve much greater apparent resolution than the native resolution of the printhead. Greyscale also allows better control of drop volume to help tune ink volume to the media requirements.
Customers can now choose a printhead based on their application needs. Drop optimization technology encompasses a range of drop formation options, each with specific features. For example, a variable drop printhead allows users to easily choose a drop size (or sizes) for the job, both in terms of image quality and substrate flexibility. The drop size determines the image resolution and actual dpi. By tuning the options, printer manufacturers can design the printer to produce small drops for high-quality photographic results and close-up viewing, or larger droplets for high-speed coverage on billboards or other signage. The choice is up to the user, and the range of drop sizes means one can manage dot gain to enable printing on a wide variety of media—from glossy paper to other materials, such as card, vinyl, etc.
That said, printheads can deliver a number of important features that may not be evident immediately. A significant trend in wide-format digital printing is printing onto textiles, also known as soft signage. Traditionally, wide-format printing involves printing onto vinyl (or rigid surfaces on flatbed printers) using ultraviolet- (UV-) cured inks. Ecological drivers, such as the reduced shipping weight costs of textiles versus vinyl, have led to the growth of soft signage. To handle an increase in soft-signage printing, new and upcoming printheads must be capable of jetting the aqueous inks required for textile printing. Certainly, beyond traditional print operations, printheads
have extended applications in areas such as packaging and ceramics. However, some of the more traditional print applications will benefit from even faster and higher quality printheads.
Today, signs and displays are printed on a wide variety of substrates. With untraditional materials that have larger non-flat surfaces, more edges and, even fibres, printheads need to be more robust and high quality, but with larger throw distances. It is helpful if the printhead is capable of printing at several millimetres away from the substrate. An optimized nozzle guard supports automated maintenance routines, which is perfect for use in harsh factory environments. Printheads need to be robust and capable of performing reliably in a range of environments (e.g. wet, dusty, hot, or cold).
Keep the ink in circulation
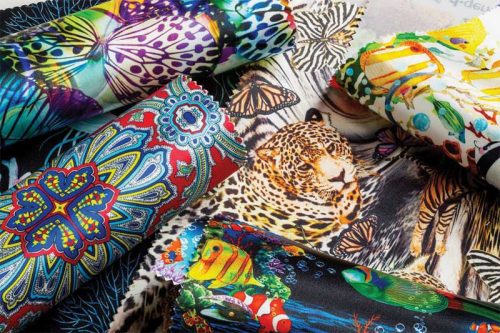
To handle an increase in soft-signage printing, new and upcoming printheads must be capable of jetting the aqueous inks required for textile printing.
The highest ink flowrate is necessary to ensure the nozzles are continuously primed, which keeps the printhead operational and the nozzles firing.
Ink recirculation in the printhead together with its unique side-shooter architecture enables ink or other fluids in the device to flow directly past the back of the nozzle during drop ejection, at very high rates. The ink or fluid is in constant motion, preventing sedimentation and nozzle blocking, particularly in heavily pigmented inks. Air bubbles and unwanted particles in the ink are carried away, radically improving reliability, even in the harshest industrial environment.
This technology also minimizes temperature variation across the printhead, as heat is removed directly from within the actuator channels, virtually eliminating print density variations. Ink viscosity is also controlled like the temperature, delivering uniform printing across the swathe and throughout the print job.
When the nozzles are not ejecting ink, either due to the nature of the image being printed or because the printhead is idle, the ink can remain in the actuator chambers for a long period, causing unpredictable changes in its properties (e.g. temperature, viscosity). This may lead to colour differences and reliability issues as the nozzles start firing again. To overcome this problem, scanning printers incorporate maintenance stations on one or both sides of the machine to keep nozzles primed with fresh ink to allow them to fire.
This ink recirculation delivers a significant step forward in running inkjet systems reliably for a full shift with minimal maintenance. Further, running costs are cut down because downtime and ink waste are reduced.