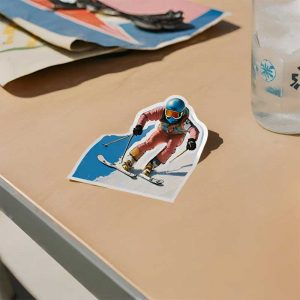
Pressure-sensitive adhesives (PSAs) are multifaceted substances with intricate chemistry and a wide variety of applications. Photos courtesy General Formulations
By Jay Kroll
Pressure-sensitive adhesives (PSAs) are multifaceted substances with intricate chemistry and a wide variety of applications. To help understand their functionality, it is best to begin with a little hands-on experiment.
If you have a sticker material nearby, grab it and cut it into two small pieces. With the first piece, peel off the paper backer (release liner) and ever-so-gently set the material down on a hard surface, making sure to not push or press it at all. Now, take the second piece and repeat the process, but this time, push down really hard—all over the material.
Count to 10. Now, peel them up. What do you notice about the two samples?
Practically every adhesive-backed graphic film incorporates a PSA. It is an integral part of any pressure-sensitive media or tape. The PSA is often an unseen component of the product, as the middle layer of pressure-sensitive media is sandwiched between the face stock and the liner. Many PSAs are clear and, therefore, not easily detected. On tape products, the adhesive is between the two layers of face stock in a roll and is often taken for granted. As long as the tape sticks during application, the adhesive is not given much notice because it is doing its job. However, if a pressure-sensitive product fails, the adhesive is usually assumed to be the culprit. Most of the time, the PSA is not the primary reason for an adhesion failure, but unfortunately, it is the easiest component to blame.
A PSA is a material that will hold two surfaces together solely by surface contact. This bond is accelerated when pressure is applied to the adhesive. PSAs are able to bond a wide variety of materials such as papers, plastics, metals, wood, and glass. They are an interesting sort of solid material (considered a “dry solid”) which is sticky without needing to be activated with water (such as a stamp or wallpaper paste) or heat (such as a thermal laminate or an iron-on patch). PSAs can be used as replacements for screws, rivets, nuts and bolts, clips, and many other physical fasteners. Their ease of application makes them worthy of consideration in many manufacturing processes and makes pressure-sensitive media an ideal choice for point-of-purchase (POP) applications and general-purpose graphics.
Many chemical materials (polymers) have been considered for use as PSAs over the years, and natural tree gums were among of the first materials to be used as adhesives. While certain tree saps have some initial pressure-sensitive properties, they usually dry out or oxidize quickly and lose their tackiness with any exterior exposure. Over time, synthetic polymers have been identified to possess the properties required to perform as a PSA. Some of the more common pressure-sensitive polymers are made with acrylic, rubber, and silicone.
Acrylic
Acrylic pressure-sensitive polymers are widely used in the manufacturing of PSAs. When polymerized, typical acrylic monomers such as acrylic acid, methyl methacrylate, 2-ethyhexyl acrylate, and butyl acrylate will form permanently tacky acrylic polymers. They are processed in a reactor under heat and pressure, for specific amounts of time and with certain catalysts, to produce acrylic pressure-sensitive polymers. Acrylic PSAs offer great clarity, good colour stability, better resistance to oxidization, and higher resistance to heat and ultraviolet (UV) radiation. Acrylics bond well to polar surfaces such as metals, glass, polyester, and polycarbonate plastic films. A disadvantage of acrylic PSAs is their low bond to materials with low surface energy, such as polyethylene or polypropylene. Overall, acrylic PSAs have good general-purpose physical properties, including a balance of peel and shear properties that enable them to be used in long-term exterior applications. The unlimited variability in formulation and choice of monomers make acrylic polymers ideal for most PSA applications.