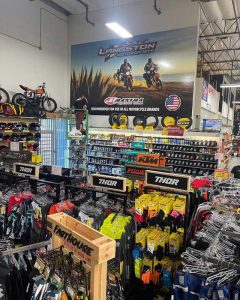
Their ease of application makes pressure-sensitive media an ideal choice for point-of-purchase (POP) applications.
Types of PSAs
Another property associated with a PSA is the type of adhesive. To obtain a smooth and consistent thickness, PSAs are coated while they are in a liquid or extremely low viscosity, and then converted to a solid. The most common types of commercially available PSAs are solvent, emulsion or water-based, hot melt, and energy-curable (UV) adhesives.
Solvent
When a PSA is solvent-borne, the adhesive resins and components are dissolved in solvents such as ethyl acetate, toluene, isopropyl alcohol, heptane, and methyl ethyl ketone (MEK) to form a liquid. This liquid is then coated, and the solvent is evaporated by heat to form a smooth, consistently thick layer of PSA. Acrylic, rubber-based, and silicone resins can all be manufactured as solvent-borne PSAs. They are easily formulated and can be additionally cross-linked to meet just about any application requirement. Solvent-based acrylics can be formulated for great chemical and heat resistance, as well as UV light resistance, which enables them to be considered for long-term exterior applications. Solvent-borne PSAs have a higher adhesive manufacturing cost and require special processing steps to control solvent emissions. However, they can be considered high-performance adhesives.
Emulsion or water-based
In an emulsion PSA, the resin and additives are dispersed in water to form the liquid adhesive. While acrylics are the most common emulsion PSAs, rubber and silicone resins can also be produced in an emulsion version. As previously mentioned, the adhesive is coated in liquid form and heat is applied to evaporate the water, leaving the solid adhesive. While emulsion PSAs continue to evolve and performance improves, the use of additives to manufacture the adhesive can affect performance. Wetting agents, surfactants, thickeners, and defoamers all remain in the adhesive in its dried state. Wetting agents and surfactants are water-sensitive and can scavenge moisture back into the PSA, acting as a plasticizer and reducing the holding power of the adhesive. This can be temporary depending on environmental conditions, but repeated cycles of exposure can reduce long-term performance. The manufacturing costs of emulsion adhesives are usually lower than solvent-borne adhesives and do not require the capital outlay or ongoing costs of emission control devices. Overall, emulsion PSAs are very competitive for removable, short-term, and general-purpose applications.
Hot melt
A hot melt PSA is a 100 per cent solid adhesive that becomes low in viscosity and takes on a liquid-like flow when it is heated. While in this state, it is coated and rapidly cooled before laminating to a heat-sensitive stock. The typical thermoplastic elastomers used as hot melt PSAs are SBCs. As they are rubber-based resins, hot melt adhesives have generally poor high-temperature resistance and will return to the flowable condition as temperature increases. Hot melt adhesives are generally used for interior applications where they are not exposed to high temperatures or UV radiation.
Energy curable
An energy curable PSA is another 100 per cent solid adhesive. The most common type uses UV radiation curing. UV-curable PSAs are a complex mixture of oligomers, monomers, photoinitiators, and additives. This results in a wide range of PSA formulations, equipped to meet any application. Additionally, processing conditions can affect the cross-linked density of the PSA, thereby changing the physical properties of a specific UV-curable formulation. Since they are thermoset adhesives after curing, UV-curable PSAs offer great high-temperature and chemical resistance, holding power, and moisture resistance. They also do not require emission control equipment, as most of them are 100 per cent solid.