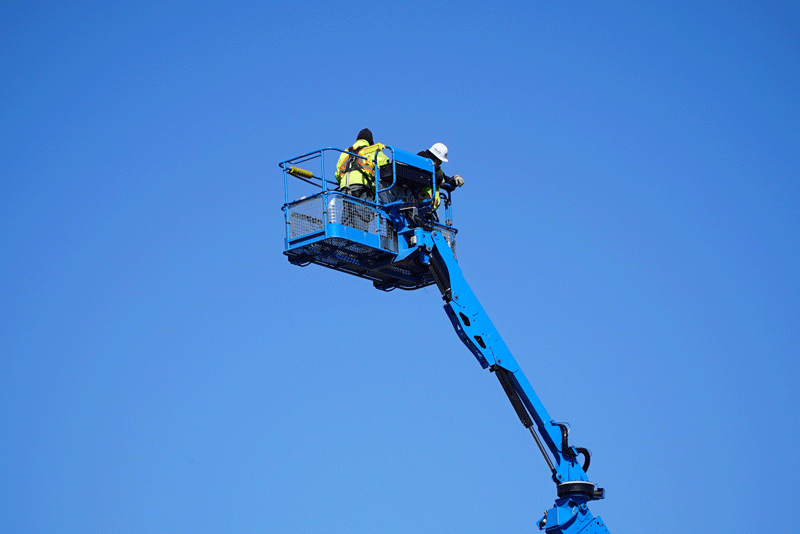
Choosing the right equipment for the installation ensures the sign is placed with precision, stability, and durability. Photos courtesy Boris Kaminsky
Maximize your installation with essential tools and safety insights
By Boris Kaminsky
Installation equipment is the backbone of signage projects. It goes beyond simply placing a sign; it ensures it is installed with precision, stability, and durability. The right tools and machinery are crucial for handling various sign sizes and types, from large, heavy installations to more delicate components. Equally important is the safety gear that protects installers and maintains a secure work environment. Properly selected and expertly used, installation equipment enhances the sign’s visual impact and ensures its longevity.
Lift and shift
Different methods are used when transporting signage products depending on the sign’s size, weight, and complexity. Here are some common forms of transportation for signs:
- Flatbed trucks: Ideal for large, oversized signs, such as pylons, channel letters, and monument signs. Flatbeds provide open space and flexibility, reducing the risk of damage.
- Box trucks: Enclosed trucks that protect smaller signs or multiple sign components from weather conditions. They are often used for medium-sized signage and light displays.
- Cargo vans: Suitable for small signs or delivering individual components. They are flexible for quick deliveries in urban areas or for local projects.
- Crane trucks: For heavy signs, especially for on-site deliveries, where the sign may need to be lifted for installation immediately upon arrival.
-
Courier, rail, and air freight services: Couriers—such as UPS—handle small-scale signage. Rail is economical for large, long-distance signs. Air freight ensures rapid delivery for urgent, high-priority shipments.
-
Freight shipping (LTL/FTL): When sending signs over long distances, freight shipping (Less Than Truckload or Full Truckload or LTL/FTL) may be used. It is particularly useful for national clients or out-of-province/state deliveries.
Each option is chosen based on cost, speed, and the need to protect the signs from damage during transit.
Raise and brace
Sign installation comes with its own set of challenges, from working at heights to handling electrical components. It’s important to stick to industry best practices to keep things safe. Even if sign industry professionals are familiar with these safety guidelines, a quick refresher can be helpful. Here’s a straightforward rundown of the eight essential safety practices every installer should keep in mind:
- Personal Protective Equipment (PPE)
Hard hats are essential for protecting against falling objects, particularly when working at heights. Safety glasses prevent eye injuries from debris, dust, or splinters during cutting or drilling. High-visibility clothing enhances visibility in high-traffic areas or construction zones. Safety gloves shield hands from cuts, abrasions, and sharp edges while handling materials and tools. Steel-toe boots provide protection against heavy falling objects and punctures. Hearing protection, such as earplugs or earmuffs, is necessary when operating loud machinery such as drills or saws.
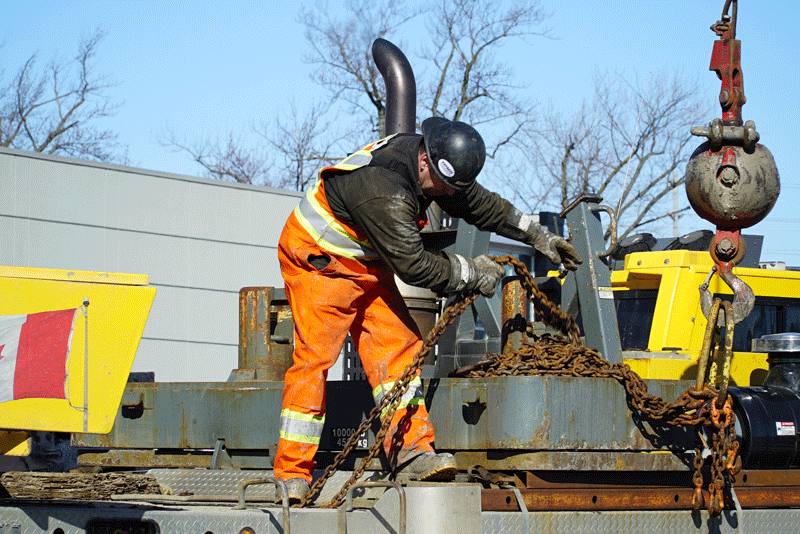
Efficient manual handling requires lifting heavy objects with proper techniques to avoid back injuries and using teamwork or mechanical lifting aids for oversized signs.
- Working at heights
Fall protection systems, including harnesses, lanyards, and lifelines, are crucial when working on ladders, scaffolding, or lifts. Scaffolding should be securely constructed and anchored, with workers always wearing fall protection while on it. Aerial lifts, such as boom and scissor lifts, must be operated with proper training and secure harnesses, and the lift should be on level ground. Ladders used should be no taller than 1.83 m (6 ft).
- Electrical safety
Lockout/tagout (LOTO) procedures are important to de-energize electrical systems before working on or near them. Use insulated tools for handling electrical components and ensure all connections meet local codes. Properly ground electrical equipment and signs to prevent shocks. Regularly inspect power tools and cords for wear, damage, or fraying.
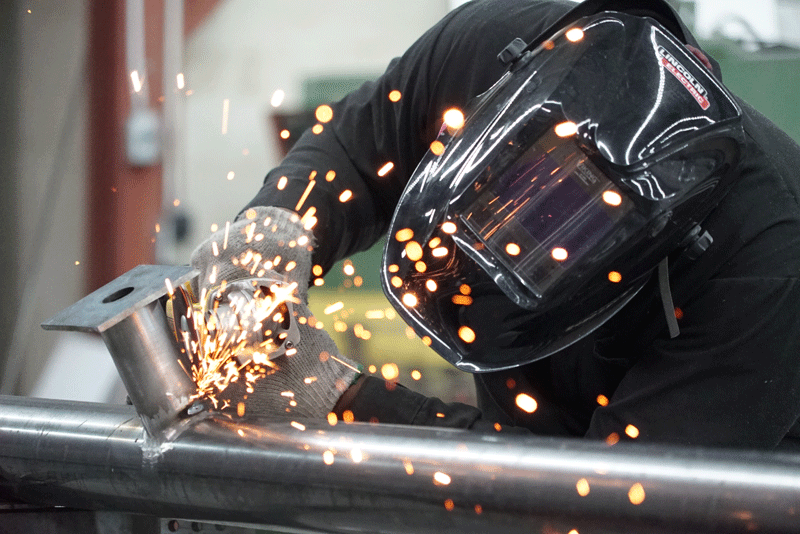
From working at heights to handling electrical components, sign installers must gear up and stick to industry best practices.
- Safe handling of materials
Efficient manual handling requires lifting heavy objects with proper techniques to avoid back injuries and using teamwork or mechanical lifting aids for oversized signs. Mechanical lifting equipment such as cranes and forklifts should be used for large or heavy signs, with operators trained and certified. Securing loads involves ensuring that signs or materials are properly secured during transportation to prevent shifting or falling.
- Hazard awareness and site safety
Call utility services to locate and mark any underground utilities, such as gas, water, or electrical lines, before digging for sign foundations. Set up traffic control using cones, barriers, or signage to manage traffic around the worksite, especially near roadways. Monitor weather conditions to avoid working at heights during high winds, rain, or storms, as lightning can pose a risk. Conduct a site inspection to check for uneven surfaces, obstructions, or hazards that could cause trips or falls on the job site.
- Proper use of tools and equipment
Tool safety requires using the right tool for each job and regularly maintaining and inspecting tools to ensure they are in good working condition. Power tool training is essential, with workers needing to be trained in the safe operation of power tools such as drills, saws, and grinders. Guardrails and barriers should be installed as temporary measures to prevent accidental access to areas where heavy tools or materials are being used or moved.
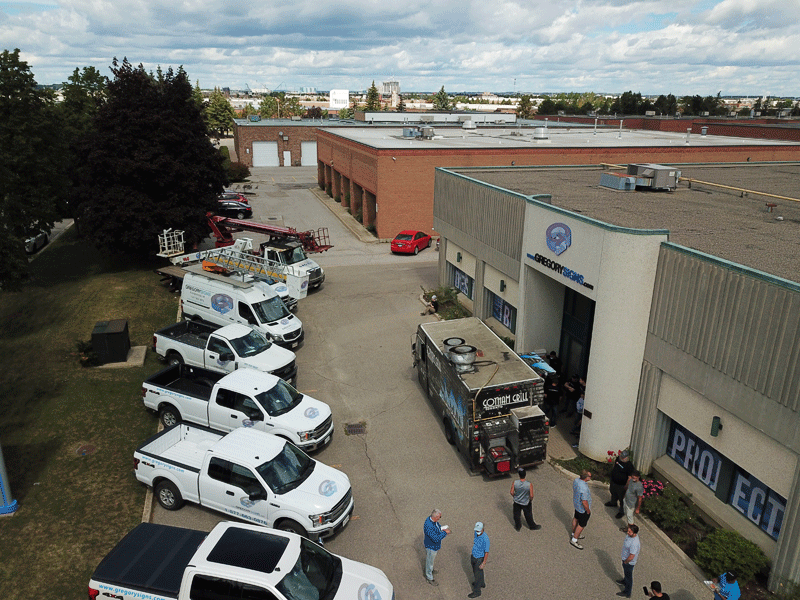
Each transport option is chosen based on cost, speed, and the need to protect the signs from damage during transit.
- Emergency preparedness
Keep first-aid kits on-site and ensure workers are trained in their use, with certified personnel in first aid and CPR. Place fire extinguishers where needed, especially near electrical equipment or welding tools. Implement an emergency evacuation plan and ensure all workers are familiar with exit routes and procedures.
- Training and certifications
Sign installers should be familiar with the Occupational Health and Safety standards, have Working at Heights Certification for fall protection and equipment use, and Electrical Safety Certification to handle electrical components safely.
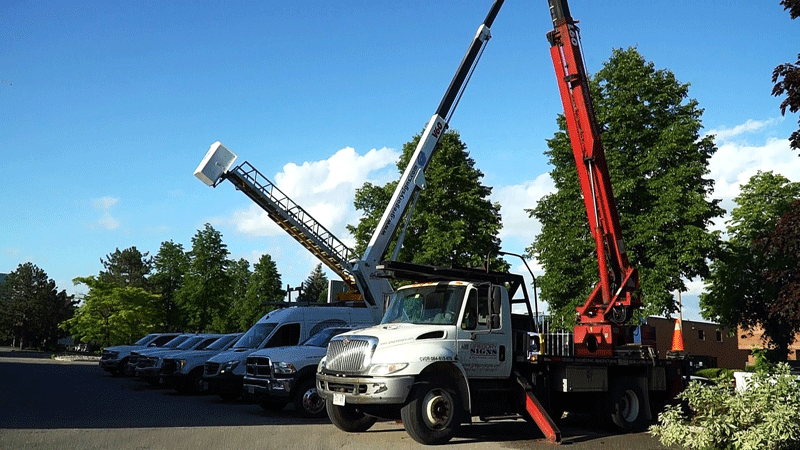
When transporting signage products, different methods are used depending on the size, weight, and complexity of the sign.
By adhering to these safety essentials, sign installers can minimize the risks associated with their job and ensure a safe work environment for themselves and their team.
Boris Kaminsky is the vice president of sales and marketing at Steel Art Signs and Gregory Signs. With 24 years of experience, he has played a key role in developing new business and managing major accounts, significantly shaping the market presence of both companies.