Wide-format Graphics: Transfer vs. direct dye sublimation
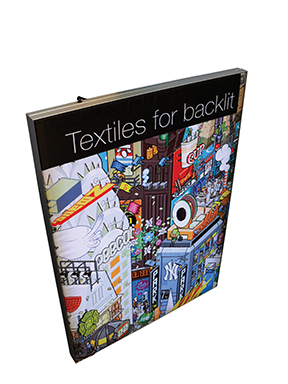
By John Selfhout
The mix of attendees and exhibitors at the recent 2014 Specialty Graphic Imaging Association (SGIA) Expo clearly showed there is widespread interest in—and creative possibilities for—printing graphics on textiles. Transfer-based and direct disperse options for dye sublimation are now well-developed processes for printing fabric graphics in brilliant colours and high resolution that are durable and washable and will drape and handle well. Both of these processes are very similar, but the differences between them are nevertheless significant and, given they call for their own dedicated equipment, signmakers will generally have to choose which of the two is best for their purposes. In this respect, there are many aspects to consider before a well-balanced decision can be made.
Transfer
Transfer-based dye sublimation is an older method, originally developed before digital printers were available. Today, it is accomplished with digital printing technologies, yet the basic process has not changed significantly.
First, the graphics are printed onto a specially coated paper. Then, the printed images are transferred to a polyester-based material—which may be a woven or knitted fabric or a non-woven substrate—under pressure and high temperature for a specified period, using a heat press or rotary calender and special protective paper. The better the degree of control over these parameters is, the better, more consistent and more reproducible the results will be.
This technique works due to the specific characteristics of both the dye sublimation ink and the fibres of the uncoated substrate. The dye sublimation ink comprises solid particles dispersed in water, oil or a solvent, which acts as a carrier for the ink particles. The four basic ink colours of cyan, magenta, yellow and key/black are sufficient for creating any combination of colours in the graphic.
One key characteristic of dye sublimation ink particles is how they transition from a solid to a gaseous state when they are heated. Most materials can exist in three states, including solid, aqueous and gaseous, but these inks never become aqueous, which makes it easier to control the process of transferring them from the paper into the textile.
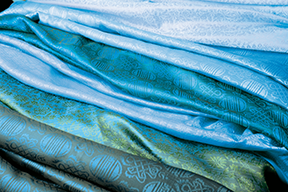
As mentioned, the nature of the fibres plays an equally important role. Unlike natural fibres, these manmade fibres are created by melting polymers and using pressure to force them through nozzles in their liquid state. High- quality fibres can be achieved with this well-established process, but they will include amorphous areas, including micro-pits and holes.
The amorphous areas are where the dye sublimation ink molecules can find sufficient surface area to connect to the polymers. The result is a permanent, irreversible connection between the inks and the polymers, since the substrate is dyed deep within its fibres, rather than simply adhering graphics to its surface. In this way, brilliant colours can be achieved without changing the feel or handle of the textile—and the material can be washed without threatening the integrity of the graphics.
With today’s digital technology, the transfer-based dye sublimation printing process also relies on a raster image processor (RIP) software package to prepare the images at the beginning. And then, following the printer, transfer paper and heat press or rotary calender, the process may also require a cutter or a sewing machine, depending on the intended final product.