By Joe’ Lloyd
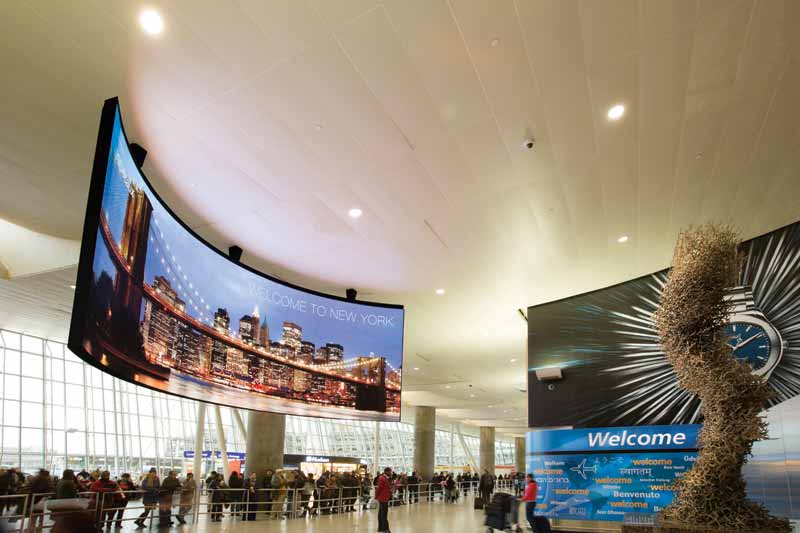
Subcomponent boards flex along curved frames, eliminating the visible seams between rigid boards and effectively locking out dust, debris, moisture, and other contaminants that can negatively affect the display’s performance.
When creating a digital display to optimize customer engagement, it is essential the solution excludes any elements that can remove audiences from the space. Some examples include dead pixels, discoloured tiles, and glitches in content. Each of these malfunctions has something in common—they all represent an interruption. Bezels, too, are interruptions. These are the cross-hatch lines that segment liquid crystal display (LCD) video walls and though they are not a breakdown of technology, they are inherently an agent of fragmentation. So are facets, the curved-display analogue of flat-surface bezels. It is these facets that disrupt the immersive efforts of any non-curved display attempting to pass off as curved.
Facets are to digital content what a screen door is to a porch; one can try looking outside, but the view is disrupted by the screen. On a faceted display, audiences can see the content, but they can also see the facets, undercutting the level of immersion the content can achieve. Beyond this blow to immersion however, it is less obvious what differentiates a faceted display from a curved one. There are a variety of design-, manufacture-, and performance-related problems that arise when working with a faceted display solution; it is important these potential challenges are explained to buyers.
Frame-skin topology
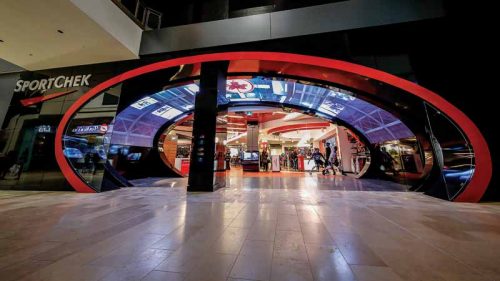
Buildings such as airports, shopping malls, sports arenas, and corporate campuses often feature atypical architectural elements that complicate the display integration process and, while a faceted facsimile will not necessarily align flush in these spaces, displays built with curved boards will.
The word ‘curved’ is often used inaccurately in the light-emitting diode (LED) industry. Many manufacturers claim to create a curved display, but the fact is, almost none of them actually do. Nearly every company creates these ‘curves’ by aligning flat, rigid displays next to one another at an angle. This leaves slight visible seams—the facets between adjacent boards that are susceptible to dust, debris, moisture, and other contaminants.
Truly curved displays make use of ‘frame-skin topology’ in their manufacturing. This means, a curved frame of a display is built first and then ‘skinned’ with subcomponent boards.
These boards flex along curved frames, eliminating the visible seams between rigid boards and effectively locking out contaminants that can negatively affect the display’s performance. This manufacturing process allows curved displays to be embedded flush into unique wall surfaces, giving architects, designers, customers, and integrators greater creative freedom with where they install their product. Buildings such as airports, shopping malls, sports arenas, and corporate campuses often feature atypical architectural elements that complicate the display integration process and, while a faceted facsimile will not necessarily align flush in these spaces, displays built with curved boards will.
A curve, when done seamlessly, has a greater esthetic effect. For example, a massive LED ring installed in a corporate lobby would not have the same impact on its audiences if it were faceted.
Here, the goal is to convey a sense of connectivity. Therefore, in this case, a technology free of any interruptions would be a more suitable choice.
There is an alternative LED solution that can approximate this level of malleability, but is not particularly suited for most direct-view uses. While a traditional LED display mounts pixels onto solid boards or tiles and then mounts those onto cabinets or frames, a transparent display instead typically mounts pixels right onto a thin, skeletal grid or flexible mesh. In theory, this framework is designed to allow viewers to see through the gaps in the grid to objects on the other side of the display, thereby rendering it effectively transparent. The flexibility of the mesh allows users to display their content onto curved glass surfaces, but at present, the technology is best used for creating ambience rather than any robust application.