The next generation
The blue colour and angularity both remain part of Viva’s visual identity to this day, but with the development of the VivaNext projects—which will include not only the aforementioned busways, but also light-rail transit (LRT) lines and extensions of Toronto Transit Commission (TTC) subway lines—has come a need to ‘refresh’ the look and feel of Viva’s existing signage and graphics. This has involved updates to a variety of wayfinding products and systems, which Entro was commissioned in 2011 to design.
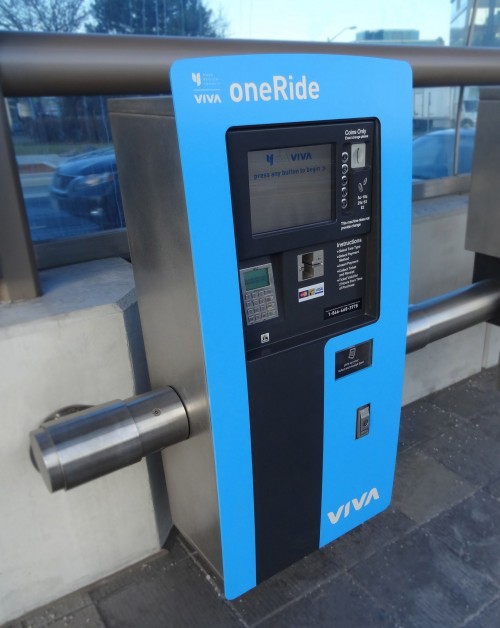
The fare-payment machines’ design was updated for minimal space requirements, modularity, dynamic load conditions and durability.
The project required a multidisciplinary work approach, from the industrial design of various new products to the structural design of site identification signs to the graphic design of wayfinding messages.
All of the service platforms, stations and towers along the dedicated busways feature new more modernized architectural designs, with a curved blue glass canopy stretching along the length of the platforms and stations. Since the signage updates were intended to reflect this style, materials similar to those used for the new bus platforms were chosen for the signs, to complement the architectural work.
Entro primarily used blue polycarbonate and stainless steel to create the main ‘fin’ signs that serve to identify each VivaNext station. These signs are the first point of contact for customers, so their visibility is crucial to the program’s success.
One of the major challenges, given the identification signs had to remain effective during both daytime and nighttime hours, was to determine the best number and most visible colours of vinyl films—which would be sandwiched in the polycarbonate—for both illuminated and non-illuminated viewing conditions. Illumination can severely affect the perceived colours of vinyl films, so extensive testing was required to find the best combination of materials.
WSI Sign Systems, based in Bolton, Ont., was tasked with fabricating and installing the station identity signs. Meanwhile, Zip Signs in Burlington, Ont., was tasked with fabricating and installing on-platform signage.
The blue glass was carried into many of the products. Also, due to the limited floor space available on the dedicated busway platforms, one of the most challenging aspects of the project was determining how to mount the signs, fare equipment and graphic elements onto the curved glass structures. In the end, Entro designed many of these products with curved elements, such that they could conform to the curved glass walls. And in conditions where it was impossible to mount products directly to the glass—due to either structural or esthetic concerns—alternative installation methods were devised.
Fare-minded
Entro was also called upon to develop a new design for the VivaNext fare equipment, which allows passengers to buy a ticket before they board the buses. (YRT introduced this proof-of-payment scheme for Viva from the start, to speed up boarding.)
To maintain consistency across the system, the same fare-payment technology used in the older Viva equipment was adopted for the new machines, but Entro was tasked with updating them, both in terms of minimizing their size for installation on narrower platforms and in terms of complementing the new branding and architecture. So, the aim was to make the equipment slender and sleeker, while incorporating some of the VivaNext architectural features to create a unified design.
There were other aspects of the project, however, that posed additional challenges. For one thing, the design intent was to develop a product that could easily be modified in the future if needed. So, provisions were included in the final mounting designs to allow the equipment to be moved or repositioned, in the event additional equipment is required in the future.
Secondly, the weight of the machines would vary depending on the number of coins inserted in them. In fact, the weight difference between an empty machine and a full machine can be as much as 272 kg (600 lb). The structural elements of the design had to accommodate for these dynamic load conditions.