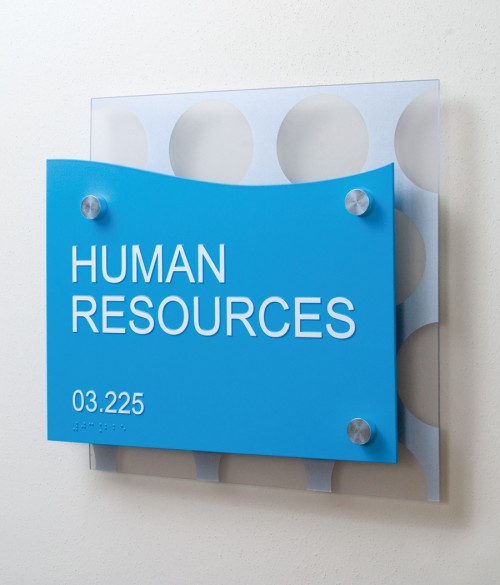
Once photopolymers have been processed, signs can be fabricated and decorated with the same conventional methods used for other typical substrates, including cutting, routing and painting. Photos courtesy Nova Polymers
Accessibility meets creativity
Accessibility signs are an integral part of a building’s interior décor. So, as interior design has evolved, signs have changed to match. While their core function is wayfinding, they can also enhance a facility’s design.
Photopolymer substrates have evolved to meet these needs. Some of the clear versions allow for both first- and second-surface decoration. Some thinner-gauge varieties can be flexed to fit into curved-frame systems.
Most photopolymer substrates are intended only for indoor wayfinding sign systems, but a few are also designed for outdoor installation. It is important to specify a resin that will not swell in a moist environment, even if the finish coat is less than perfect. Otherwise, the sign could eventually collapse.
Design options include simulating natural and organic materials, solid colours, marble finishes and wood grain patterns, among others. Photopolymers can achieve this versatility by incorporating specialized laminates as their base substrates.
While photopolymers with a clear PETG base provide design advantages, as mentioned, there is still demand for substrates with an aluminum base. A brushed aluminum base can provide an attractive visual effect. Another option is a photoluminescent rigid polyvinyl chloride (PVC) base for safety and egress signs that need to remain visible in the dark.
Additional advantages
The first priority for any materials used in accessibility signs is to meet applicable code requirements. Secondly, they must meet the facility’s design needs. Photopolymer substrates have evolved for both of these purposes, but they also offer other benefits.
Sustainability
Beyond the development of accessibility sign codes, another trend that is influencing the choice of materials used in large facilities is the ‘green building’ movement. Signs can contribute in this respect, too. They can even help a building achieve a Leadership in Energy and Environmental Design (LEED) rating.
Photopolymer signage involves an inherently very eco-friendly process. As mentioned, it uses plain tap water. It emits no volatile organic compounds (VOCs) and the effluent is 100 per cent biodegradable. A PETG base generally comprises at least 40 per cent post-industrial recycled content. By way of example, 3form’s ecoresin, a co-polyester recycled-content product, is Greenguard-certified by Underwriters Laboratories (UL). Any off-cuts can be recycled again.
Durability
With photopolymer-based signs, unlike some other options for accessibility signs, the braille dots and other tactile elements are integrally bonded with the substrate and base for a high level of durability. This occurs during the exposure process, when UV light cross-links the photopolymer molecules with the surface of the substrate, creating a bond that is stronger than the photopolymer itself.
Other manufacturing methods use a ‘sheet’ adhesive to attach a series of cut-out plastic components onto the substrate. While there are many ways of adhering these signs’ letters, dots and pictograms, they all essentially involve ‘taping’ them to the surface, which makes them very easy to vandalize.
Further, the photopolymer process requires a topcoat of paint or—for patterns and graphics—a clearcoat. This finish provides an additional layer of protection for the sign, enhancing its durability in the field.