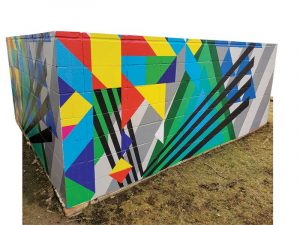
Cast vinyl is typically used for more complex, long-life projects such as fleet graphics or textured wall wraps.
All these characteristics can be designed into the product and should all be considered based on the ultimate application surface, projected lifespan, and any special performance requirements.
The final building block in the mix is the liner, which is much more than the shiny piece of paper you throw away at the end of the job. The liner thickness, paper type, and silicone formulation play a vital role in the overall product performance. Manufacturing methods may vary but, generally, the release liner is coated with adhesive, run through an oven to dry/cure the adhesive, and the face film is then laminated prior to winding into a large jumbo roll. Very rarely will the vinyl itself go through the oven, and that has to do with “memory.” Paper or film liner is stable through the adhesive coating process; if coating directly to the vinyl, it would have a tendency to soften, stretch, or shrink, and ultimately end up impossible to work with.
Liner gives a surface to cut against, provides a way to deliver stickers across the world, imparts a pattern to the adhesive to allow for air to escape during installation, and makes it so we can use and reuse removable decals. It is critical for the manufacture of adhesive-coated vinyl, and functional for how we use and install the various flavours of application-specific products. It is a highly engineered, necessary component, even if just thinking of it as the piece that gets thrown away.
So, what if you need to print window graphics for a one-month promotion at a pizza shop? One might use a monomeric or polymeric calendered vinyl, probably a low-tack removable adhesive, and a regular 90# lay flat liner with or without air egress. Cast vinyl would be overkill and using a permanent adhesive on a short-term application should be avoided.
Wall graphics might require something like a polymeric calendered vinyl with an adhesive that is both high-tack and removable, and the slight texture of the painted drywall means no special air egress functionality is needed from the liner. Cast vinyl can be used for wall wraps, but then a laminate needs to be added and it becomes really expensive for a job with less expensive vinyl options specifically designed for it.
Cut vinyl lettering for a shop window that needs to last three to five years could use a polymeric vinyl, permanent adhesive, and a 78# liner for better performance and finer detail with the cutting equipment.
These three building blocks working together—film, adhesive, and liner—represent a world of possibilities in the graphics industry. Knowing the options and materials will help to decipher the pieces and parts and allow for the right combination for the application. The goal is to understand what one is working with and be able to know “which glue is right for you” without reprints, rework, or guessing, and to ultimately be the expert for the customers to guarantee repeat business and quality work every time.
Jay Kroll is a product manager at General Formulations, a leading manufacturer of pressure-sensitive solutions for the graphics industry. His focus is on cut vinyl, transit, and wall graphic applications. He has been designing and developing various manufactured solutions for more than 20 years in the medical, aerospace, specialty tape, and graphics industries.