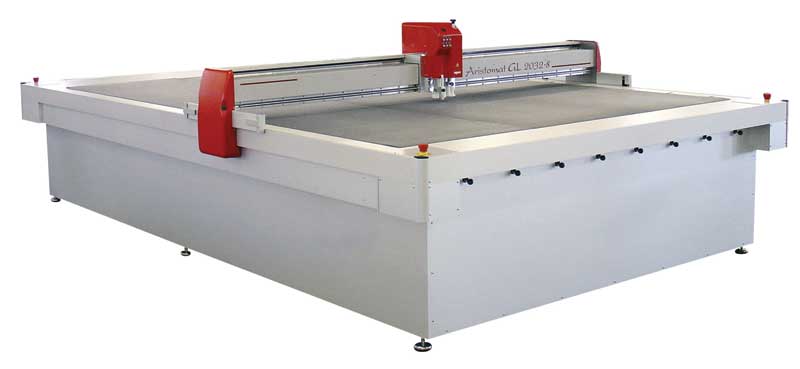
Today’s routers are highly flexible, with easily changeable cutting heads and tools.
Photo courtesy Aristo
Hardware options
Finishing options go beyond cutting. Signs also need to be mounted, pole pockets need to be sewn, banner grommets need to be installed and backlit and frontlit displays need to be framed.
Flatbed cutting tables are versatile in terms of tool options and roll adapters that enable the use of both rigid and RTR media. The size of the table will depend on the shop’s throughput requirements, but there are also double-sided beds that allow an operator to cut on one side of the table while loading the next substrate on the other side, for non-stop productivity.
With the rise of dye sublimation, cutters with special handling capabilities are now in demand. Laser cutting heads are needed to properly finish polyester-based media, by simultaneously cutting the material and sealing its edges to prevent fraying. Other cutters for aluminum, steel and polycarbonates are required to answer growing demand from industrial printing applications.
That said, lower-end RTR contour cutters account for the largest segment of the market, by far. And while the demand for specialized tools has increased, the trend begs the question: do all such needs justify their own type of cutter or would a multi-purpose machine that can handle many types of materials be a better fit?
InfoTrends’ studies show the market penetration of vinyl cutters and printers with built-in cutters reached nearly 85 per cent in 2014, while high-end flatbed cutters comprised roughly 15 per cent. As such, there are still significant opportunities for both (a) dealers selling specialized equipment and (b) PSPs offering cutting and finishing services to their fellow PSPs.
There is now a trend of sign shops replacing many smaller printers with fewer bigger ones, so as to achieve higher volumes of throughput. In response, some midsized shops are expanding their facilities and exploring options to improve their workflow.
Finishing also needs to be highly flexible to accommodate the necessary workflow changes. Wider materials, especially, have driven the addition of automated cutting, due to their size and throughput requirements. Factors like accuracy and cleanliness also come into play.
RTR cutters
In today’s market, many RTR cutters are available that are competitive in terms of price and features. They are best used to cut and score paper, canvas, polystyrene (PS), films, foils, polycarbonates, magnetic media, PVC and other vinyls. Lower-end models have been introduced for lighter-duty requirements.
Features may include self-sharpening blades, a front roll shaft to help ensure even widths, automatic-lowering pressure bars to hold materials in place during cutting, automatic optical registration crop mark sensors for additional precision and ‘half-cuts’ to leave a backing sheet that can be easily detached when necessary, e.g. for decals and stickers.
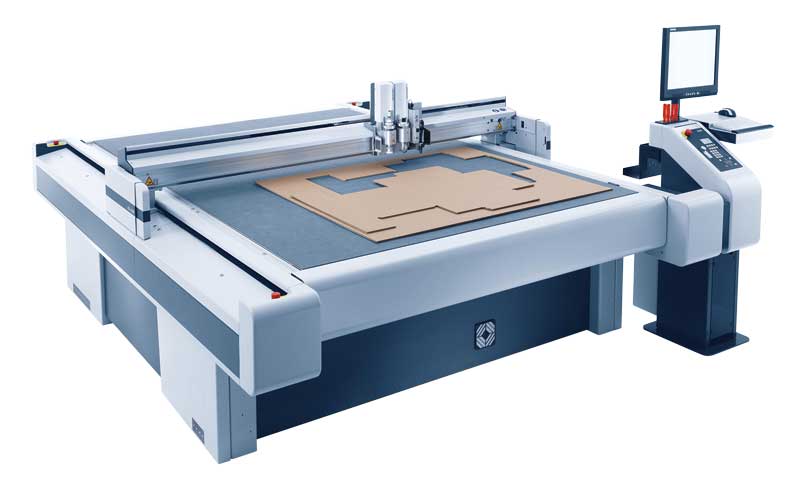
Energy-efficient vacuum pumps help optimize digital flatbed cutters for high-volume production.
Photo courtesy Zund
Cutting tables
Having expanded from the early days of woodworking sign shops, today’s computer numerical control (CNC) routers and cutting tables are equipped with easily changeable cutting heads and tools, including options for kiss-cutting, through-cutting, oscillation-cutting, V-notching, creasing and scoring. Various models can finish printed graphics, wood, metal and packaging materials.
Digital cutting technology has both increased throughput for full-time operations and made short-run prototypes and samples economically viable for wide-format and industrial printing environments. Many tables are equipped with vacuum ‘hold-down’ beds to keep substrates firmly in place after they are conveyed by belts, some of which can move materials on and off the bed automatically, to maximize productivity.
Indeed, automation is being applied to cutting just as it has to printing. Wide-format inkjet printers using raster image processor (RIP) software can be ‘cut-enabled,’ whereby they both output a cutting file and print cutting marks on the material that are then detected by machine vision registration technology, for co-ordinated print-to-cut functionality. Workflow software is also being deployed across printers and cutters to assist with pre-press requirements, job management and cost tracking.
Multi-functional tables are synchronizing cutting, perforating, marking and routing to support variable-production workflows, based on the optimal configuration for each job. Moreover, automation means loading, unloading and processing can all occur at the same time.
Some of these tables combine knife cutting with automated laser cutting, which is better-suited for fabrics and some non-PVC plastics. With this combination, virtually any material that can be inkjet-printed on a wide- to grand-format press can then be digitally cut on a table. One of the keys with regard to automation is to integrate both (a) a motorized roll unwinder to place fabrics on the table without stretching or wrinkling and (b) a board system for loading rigid sheet materials from a pallet.