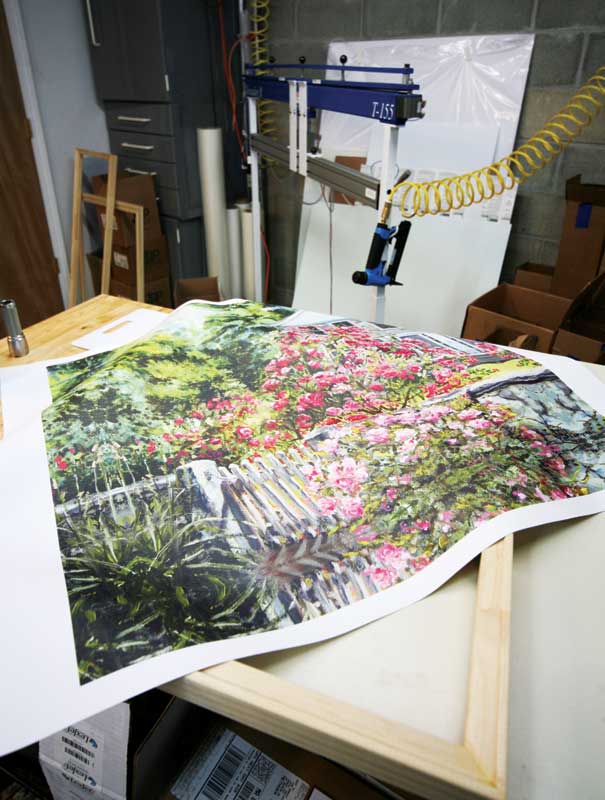
The texture of canvas is determined by the diameter of the threads used to create it and how tightly they are woven.
Polyester/cotton blends
The most common base materials overall are polyester/cotton blends. These are designed to split the difference between the esthetic qualities of cotton and the production consistency of polyester.
Most of the blends use a polyester-to-cotton ratio of 60:40, emphasizing the importance of polyester’s consistency, which ensures the first print will look the same as the 50th.
Threads
In addition to the base material, the texture of canvas is determined by the diameter of the threads used to create it and how tightly they are woven. The tighter the weave, the less visible the texture in the finished print.
The ratio of threads on the loom running in the X and Y directions also affects the texture. A canvas with a two-over-one weave has more texture than a one-over-one weave, since there are more loops per square centimetre.
It is worth noting even a highly textured base canvas may lose some of its look if coatings are applied to change the finish or make it more resistant to water or ultraviolet (UV) rays. The more coatings are applied, the more they will fill in the peaks and valleys of the material to create a smoother finish.
Weight
Inkjet-printable canvases typically range in weight from 454 to 624 g (16 to 22 oz), though there are also lighter and heavier options. A heavier canvas is more durable during stretching, finishing and handling, while a lighter canvas will usually prove more economical.
Matte
A matte finish is usually preferred for fine art reproductions and for lighting situations where glare could be an issue. The downside of a matte finish is a smaller colour gamut. If there are a lot of bright colours in a graphic that require greater accuracy, then a satin or gloss finish may be better.
That said, adding a gloss coating to a matte canvas can help make images ‘pop’ despite their restrained colour gamut. And for most applications, the colour gamut of many matte canvases is more than adequate.
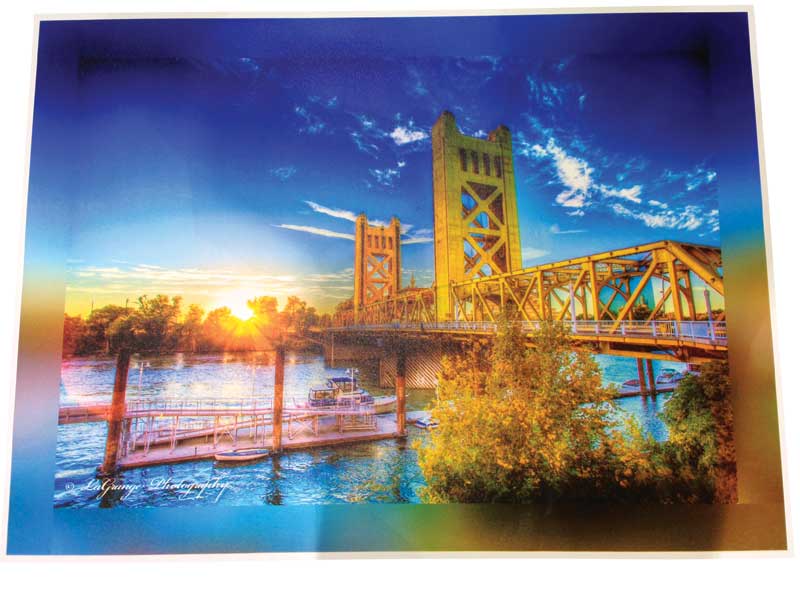
A satin finish provides a sheen that is less susceptible to glare than a gloss finish. It also expands the colour gamut.
Satin
A satin finish provides a sheen that is not as susceptible as gloss to glare and expands the colour gamut. Typically, this finish is chosen simply because the client likes how it looks.
Gloss
A gloss finish is a great option for canvases designed for use in solvent-based or durable aqueous ‘latex’ inkjet printers, since it allows the coating step to be skipped, saving time and money.
With latex printers, it is important to be extra-careful when stretching the material, as a gloss inkjet coating is more likely to crack than other finishes are.
One option for artists who prefer a matte finish, but are diligent about hitting their colours as accurately as possible, is to print to a gloss canvas and then add a matte coating.
OBAs and archiving
OBAs have been used as additives in photographic papers since the 1950s, but photographers have a love-hate relationship with them. While they increase the whiteness of the material and the colour pop of the images, they may also reduce the archival qualities of the prints.
Fortunately, international archival specifications have been developed that allow for chemical additives to brighten and stabilize printable materials. Many of the popular fine-art papers and canvases alike use OBAS and have been tested for archival quality, often obtaining 100-plus year ratings.