Wide-format Graphics: Canvas printing for sign shops
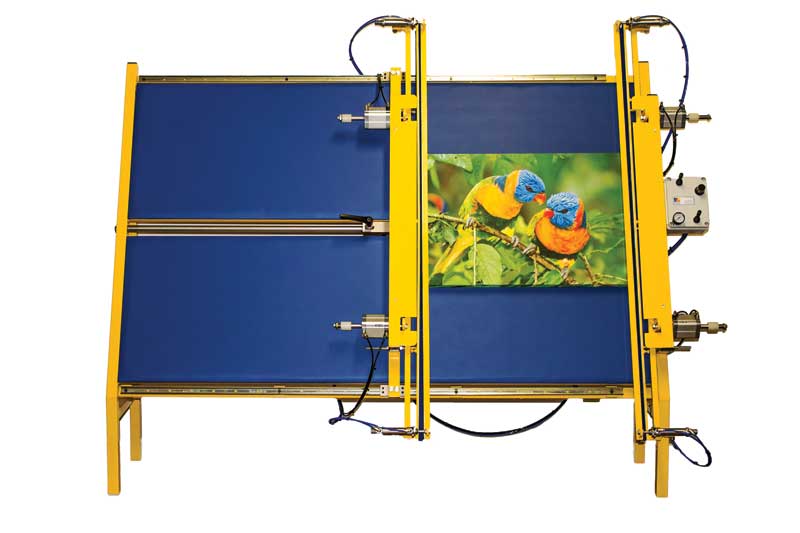
Wide-format printers
When choosing a printer for canvas, the volume to be produced is an important consideration, but so too are the sign shop’s capital equipment budget, market focus, current production and application mix, post-print finishing capabilities, desired clientele and those clients’ expectations (e.g. image fidelity vs. economical price).
The hardware choices for wide-format printing used to be fairly simple, but this simplicity also brought limitations. Over time, with the introduction of increasingly reliable and affordable UV-curing, solvent-based and latex printers, the number of potential applications that could be addressed grew and questions of print durability became less of an issue.
Each printing technology still has specific characteristics that need to be taken into account, of course, based on a sign shop’s goals, budget and operating environment. While there is no such thing as a single perfect printer, there are certainly ideal printers waiting to be used to their full potential.
Aqueous
In an aqueous inkjet printer, the ink is primarily water-based, mixed with either dyes or pigments. These devices are widely used for canvas printing and typically offer the best image quality, with pigments providing greater print durability than dyes. Indeed, pigmented inks have become the industry standard, as they eliminate much of lamination that was previously required for dye-based inks in short-term outdoor and long-term indoor applications.
While lamination may not be required, it is still recommended to coat an aqueous inkjet-
printed canvas to protect it against cracking along the edges when stretching the material, as well as against environmental factors. Liquid coatings also help enhance the texture of canvas, providing more of a ‘painted’ artistic look, and are available in gloss, satin and matte varieties.
Another advantage of an aqueous inkjet printer is versatility, as it can also provide excellent colour reproduction and graphic longevity on photo paper, polypropylene (PP), polycarbonates and fabric. (Some specialty applications, such as vehicle wraps, are more difficult and time-consuming.)
Further, these printers carry a significantly lower upfront cost than a solvent, latex or UV-curing printer—but the greatest expense, due to time and labour, is in finishing. From printing to shipping, sign shops can expect to add at least 48 hours to production, since they should wait 24 hours before coating and 24 hours before stretching. Even with automation in the finishing department, such as coating and canvas stretching machines, the lag time is an important consideration.
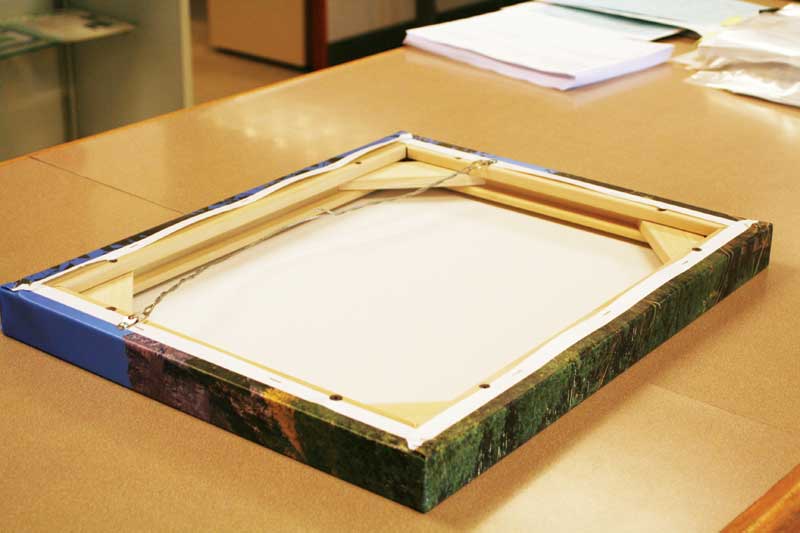
Fortunately, aqueous printers are virtually ‘plug-and-play,’ requiring very little time to tweak them for different materials. They also require little maintenance, other than keeping the production area as clean as possible. For these reasons, they are the most reliable printers over the long haul.
Aqueous printing is also arguably the environmentally friendliest wide-format technology. The inks are water-based and their cartridges are easier to recycle and reuse, which is also an economical benefit.
Unlike most solvent-based and UV-curing printers, aqueous inkjet printers do not need to be vented or filtered for a safe work place. Print shop employees will breathe easier.
In terms of quality, aqueous will provide a better print with a wider colour gamut at production speeds than other printing technologies, but the wider the gamut, the slower the speed. It is important to check what a printer’s speed will be in its highest-quality mode.
Aqueous printers tend to use thermal printheads that do not last as long as the piezoelectric printheads found in most solvent printers (and some aqueous photo printers). Fortunately, thermal printheads are less expensive to buy and replace.