Latex
While latex inks are also aqueous, they are more durable and scratch-resistant, such that a latex-printed canvas will generally not need to be coated. And for instances where a customer prefers the appearance of a coated print, lamination can occur right away, since the ink is instantly dry and outgassed.
The quality of latex prints has been inching closer to aqueous quality, but the difference is not a major issue anyway; most wide-format inkjet printers will produce the quality necessary for high-volume canvas decor production. Sign shops providing custom work for pickier clients should request samples from printer manufacturers or even distributors—using client-supplied files—before choosing which device to buy.
Latex ink and media costs are about the same as for other aqueous and solvent printers. No special ventilation is required to meet occupational exposure limits, there are no requirements for air discharge permitting and the printed graphics emit extremely low levels of volatile organic compounds (VOCs).
Latex printers require more maintenance than other aqueous printers, but less than a solvent or UV-curing printer.
Solvent
At a time when commercial signmakers continually complained about the outdoor durability of printed graphics, solvent printing was a godsend when it arrived on the scene. Manufacturers developed ink sets that could penetrate and permeate vinyl, whereas aqueous inks were anchored by coatings to sit on the surface of the material. If an aqueous print could be thought of as a sticker, solvent was more like a tattoo.
Most early solvent inks were caustic and could penetrate just about any material. Since then, the sign industry has moved toward lower-solvent and ‘eco-solvent’ inks, which require some level of substrate pre-treatment or coating to ensure strong adhesion.
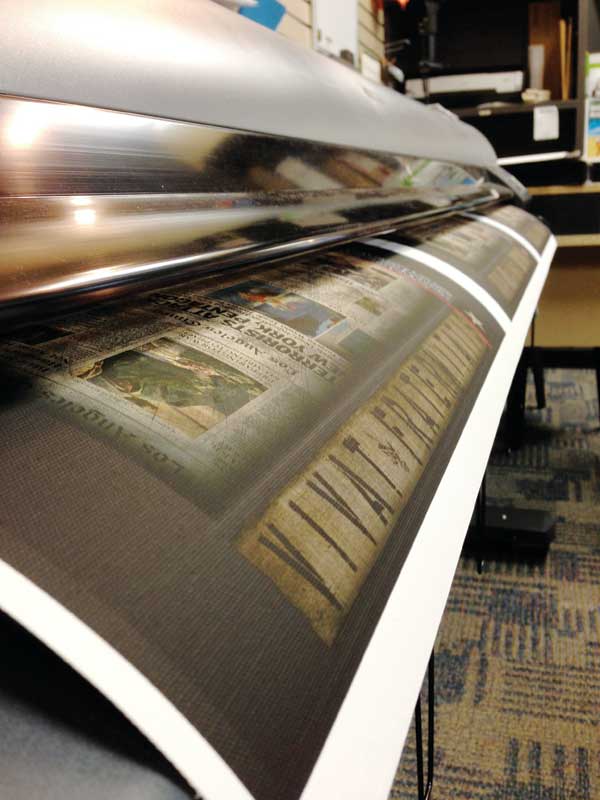
These graphics were printed onto matte canvas, wrapped on stretcher bars and finished with a satin coating.
Today, even fine-art reproduction companies have migrated to solvent printing, as it eliminates the need for post-print coatings. They can simply choose a canvas finish—i.e. gloss, satin or matte—and move straight on from printing to stretching.
There is a vast range of solvent printers available today, including some low-solvent models with prices, image quality levels and capabilities that are similar to aqueous inkjet printers in the canvas market. A solvent printer will typically cost more upfront, but carry lower ink and media expenses.
Outside of minor maintenance, typically an hour or less per month, today’s solvent printers can be run continuously. While they can produce durable graphics on canvas and other materials that do not require lamination or coatings, there is usually a recommended period for post-print drying and outgassing.
As mentioned, most solvent printers use piezoelectric printheads, which are more durable than the thermal printheads typical in aqueous printers.
UV-curing
UV-curing printing is the only wide-format technology that allows graphics to be printed directly to rigid materials, such as corrugated plastic, polystyrene (PS) display boards, polyvinyl chloride (PVC) foam boards and even doors and tabletops. The inks are cured using built-in UV lamps, so they can adhere to a wide variety of materials. Their durability rivals solvent inks and they rarely need any lamination, unless a different texture is desired or, for roll materials, additional rigidity.
The printing process usually requires an air filter, but the emissions are not nearly as voluminous or harmful as those from solvents. And in terms of environmental impact, the ability to print directly to rigid materials—rather than on vinyl that is later mounted to a rigid backing—helps eliminate material waste.
Today’s ‘hybrid’ UV-curing printers can switch from flatbed printing of rigid substrates to roll-to-roll (RTR) printing on flexible materials, but their inks are generally not designed for canvas printing. Specifically, they are not flexible enough for the stretching process (though they may be fine for mounted, pre-stretched or framed canvas prints). Indeed, almost all applications are ‘fair game’ for UV-curable inks, but the most notable exceptions are vehicle graphics and stretched canvas, both for reasons of flexibility.
With that in mind, UV-curing printers should only be considered a last resort for canvas printing. Some signmakers use them to print directly onto a pre-stretched blank canvas, but then they will usually have to paint the edges, as most clients expect either a ‘gallery wrap’ (where the image continues onto the edges of the frame, usually mirrored) or a ‘museum wrap’ (a solid colour on the edges).