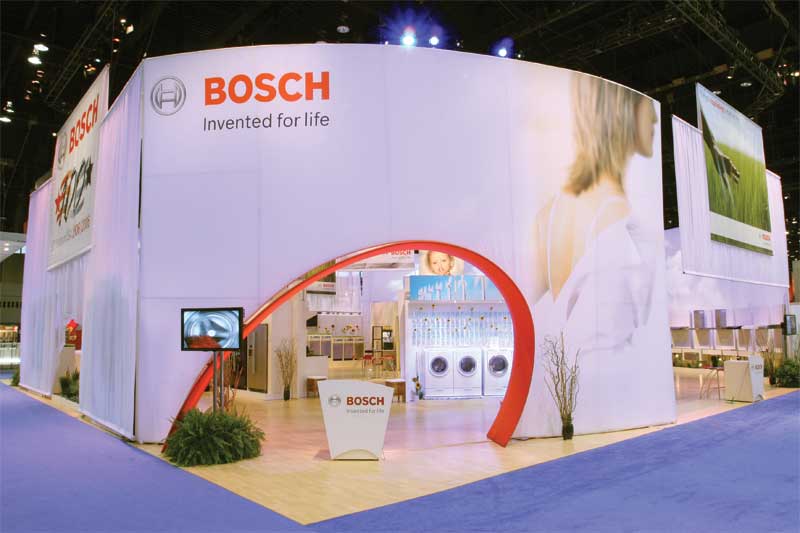
Photos courtesy Craig M. Berger
By Craig M. Berger
Digital printing is a key part of nearly every area of the sign and graphics industry. Indeed, the management of large-format printers is considered one of the most important tasks for sign fabricators today, if they are to be successful. A lack of planning in this respect can cost thousands of hours and dollars, while a successful approach to print management can foster new opportunities and innovations.
Direct-to-substrate and
layered printing
Digital printing’s direct-to-substrate and layered processes grew out of a much older technology—screenprinting, where ink is applied through a fine mesh onto such materials as fabrics, wood and steel.
An entire industry of craftspeople, schools and suppliers grew over the 1,000-year-plus history of screenprinting. And today, in product packaging and other industries that rely on large-scale manufacturing, screenprinting still plays a large role. Even in the sign industry, while digital technologies are replacing screenprinting for many jobs, it continues to be useful for large rollouts of similar graphics in a narrow colour range, such as parking signs.
In the right hands, screenprinting is renowned for crisp lines and compatibility with a wide variety of surfaces. Its growth today is hindered, however, by the need for a large investment in training and facilities.
The technology behind inkjet printing, meanwhile, has been known for more than 100 years and only became practical for commercial purposes in the 1970s. Inkjet printing became very popular in the 1990s as a low-cost approach to colour graphics, but it took another 20 years of continuous improvement before it could achieve levels of detail close to that of screenprinting and photography.
Flatbed printing added the capability to address multiple substrates without needing to change their shape or size beyond the parameters of the overall size of the bed. Many large-format flatbed printers can accommodate materials up to 51 mm (2 in.) thick, including grained woods and textured metals, although each may require a different ink ‘alchemy.’ The process has become as much of an art as a science, with sign companies experimenting with special visual effects.
The two primary types of inks for these printers have been solvent-based and ultraviolet-curable (UV-curable). Solvent inks are generally waterproof and durable for outdoor graphics, but require extensive heating during printing and time afterwards to dry. UV inks, as their name suggests, are cured quickly through exposure to light. They are considered environmentally friendlier than solvent inks, but are less durable and are susceptible to cracking. That said, there are many different formulations of both solvent and UV inks, including advanced UV inks that are effective for outdoor graphics.
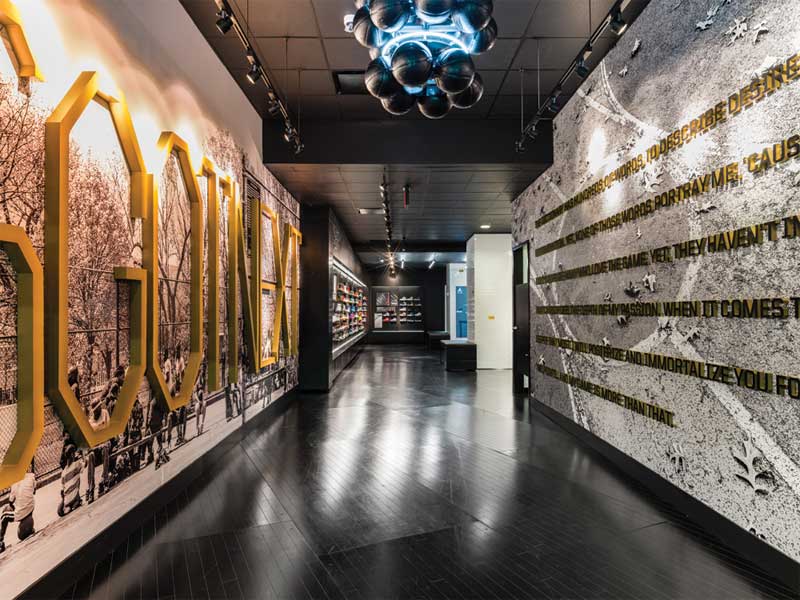
Some environments offer the opportunity to combine printed graphics with dimensional signage.
Printers that can also cut help streamline the production process. The integration of flatbed printing and routing technologies, for example, has turned the creation of printed signs into a more seamless and efficient process, particularly for the packaging industry’s printing of merchandising fixtures for retail environments.
One key attribute of direct-to-substrate and layered printing is it can be applied to dimensional surfaces of a variety of rigid and semi-rigid materials, including plastics and metals. Vacuum-formed plastic, for example, has been used to produce sign faces for at least 40 years, but only recently have both software and hardware been developed that can digitally print them successfully. The software can control for the distortions when plastic is moulded into a dimensional shape, enabling the graphics to be printed precisely.
‘Rough’ direct-to-substrate printing entails placing graphics on loose substrate surfaces, such as cork or rusted steel. This capability has found new applications in art, display and industrial settings.
Three-dimensional (3-D) printers—which create sculptural objects and can apply printed graphics to them—are still new and may have enormous future potential in the sign industry, particularly for the production of accessibility signage and complex dimensional signs. Issues with speed and durability will need to be resolved, but already, precision cast moulds based on intricate forms have been 3-D printed for the sign industry.