Wide-format Graphics: Digital printing trends and technologies in the sign industry
Direct-to-vinyl and fabric printing
Over the last 30 years, the printing of large-format graphics on vinyls and fabrics has built a complex community of fabricators, print service providers (PSPs), ink formulators and material manufacturers. Together, they have lowered the barrier to entry, to the point where even the smallest sign shops can enter the market. And while direct-to-substrate printing has addressed many of the materials used in signmaking, vinyl and fabric printing has become the industry’s primary method for covering large exterior and interior walls, windows, floors and other surfaces.
The industry standard has long been the use of white, self-adhesive vinyl as a base surface for wide-format graphics. It is a dependable substrate with extensive research and support behind it. As the use of vinyl has grown, many traditional sign installations have been replaced with large, colourful inkjet-printed graphics.
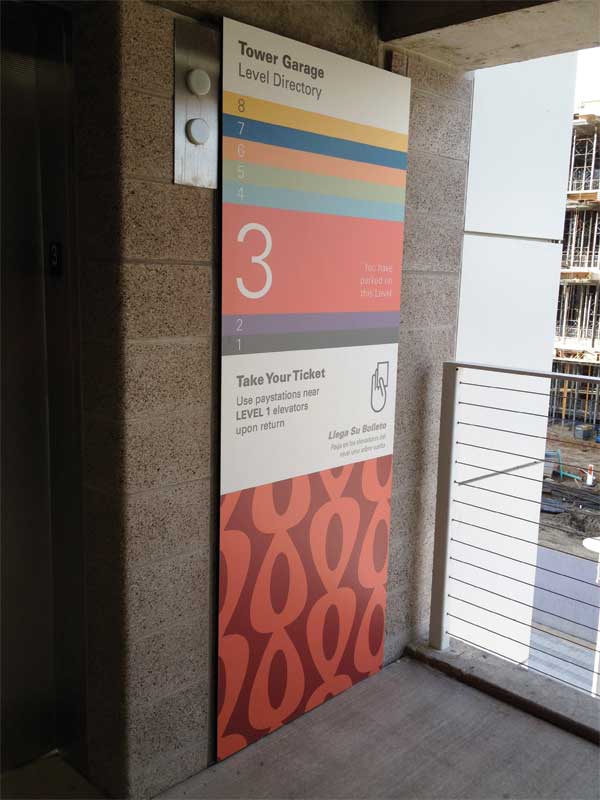
Internal illumination, for example, is a key factor for signage visibility, which has driven the development of vinyls in a variety of opacity levels, including transparent and translucent films and perforated meshes.
One major advantage of printing on vinyl is colour matching at a low price. The material is ideal for additional second-surface graphics for branded environments. Even mural design has become an entirely digital process, with specialty vinyls that can be applied with heat to rough surfaces, including brick, stone and concrete, and that will endure extreme weather conditions. These materials are being used everywhere from retail floors (with an anti-slip laminate) to parking garage walls.
Fabric manufacturers have also made enormous strides in recent years in developing textiles that can be directly printed. They do not achieve the same level of graphic durability as with dye sublimation, but the gap between the two processes has narrowed with the developing of improved inks and coatings to enhance the longevity of ‘soft signage.’
Embedded and sublimated graphics
Dye sublimation is just one example of several methods that bind inks to substrates. Long before digital printing, after all, images were baked into porcelain and powdercoated into metal. The use of heat and electrostatic energy to embed and sublimate graphics remains prevalent today in areas where long-term durability is especially important, such as with transportation and park signs. Enamel, for example, is used to create signs for the subway system in New York, N.Y.
Embedded graphics are useful not only for withstanding harsh environmental conditions for long periods, but also in terms of seamlessly integrating signage into a building’s architecture. As such, many of these processes have been developed by outside specialists, rather than companies in the sign industry that tend to focus on shorter-term promotional graphics.
Dye sublimation, for its part, is now used extensively for the production of banners, awning graphics, building wraps and other soft signage. The process uses a heat press to transfer a digitally printed image from paper to fabric. The resulting graphics are light and flexible, but also permanent.
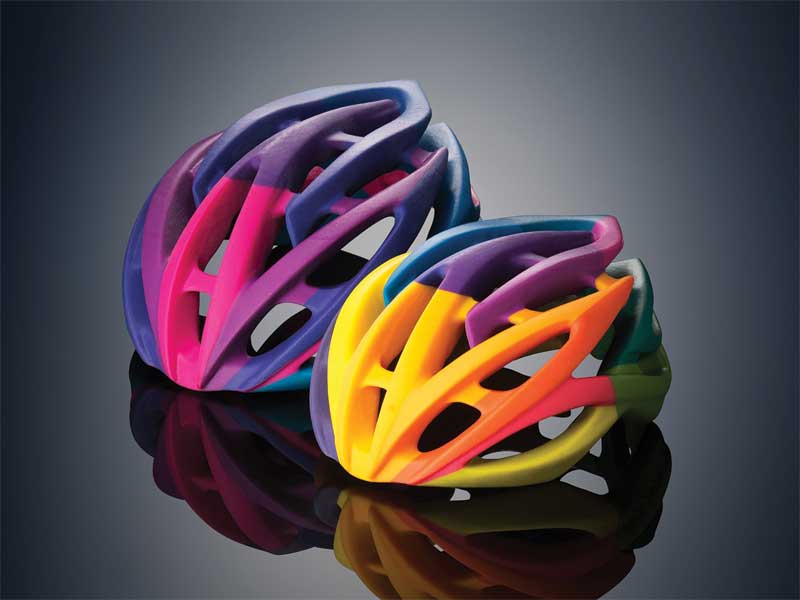
Heat and pressure can also be used to embed graphics in laminates. The resulting signs are popular in exhibitions, parks and transit systems, where tactility and durability are important. The laminates can be fabricated at a variety of thicknesses, including those thin enough to curve around surfaces.
Another process that has long been used for park and transportation signs is embedding graphics in fibreglass. The results are not as precise as with other approaches, but are highly resistant to scratching and fading.
Like laminates, powdercoated graphics have their roots in building materials. Materials that can be powdercoated include wood, glass and metal. As graphics can be applied directly to the substrate, this process has seen success with signs and information panels that are integrated directly into buildings, as well as with complex curves and other shapes, such as perforated screens.
Branded environments
Large-format digital printing has transformed
the way architects and interior designers develop interior environments. In fact, most of today’s top architecture and interior design firms have in-house design teams that specialize in branding environments with indoor graphics. They have had notable influence on the retail, corporate, hospitality and health-care sectors.
This trend has created new opportunities for sign companies, particularly those that specialize in large retail and corporate graphic rollouts, but it has also brought new, specialized competitors into the market. One of the main challenges is differentiating higher-quality inks and materials from lower-cost options, particularly for environments that require high levels of graphic durability.
“Digital printing has reshaped our business,” says Beth Gillespie, president of Acorn Sign Graphics. “We have printed on many different materials, experimented with photopolymers for accessibility signage and invested in new substrates with high recycled content and reclaimed materials. Clients expect us to provide complete ‘placemaking’ and those who are willing to invest time and resources into prototyping are creating momentum toward new, exciting applications.”
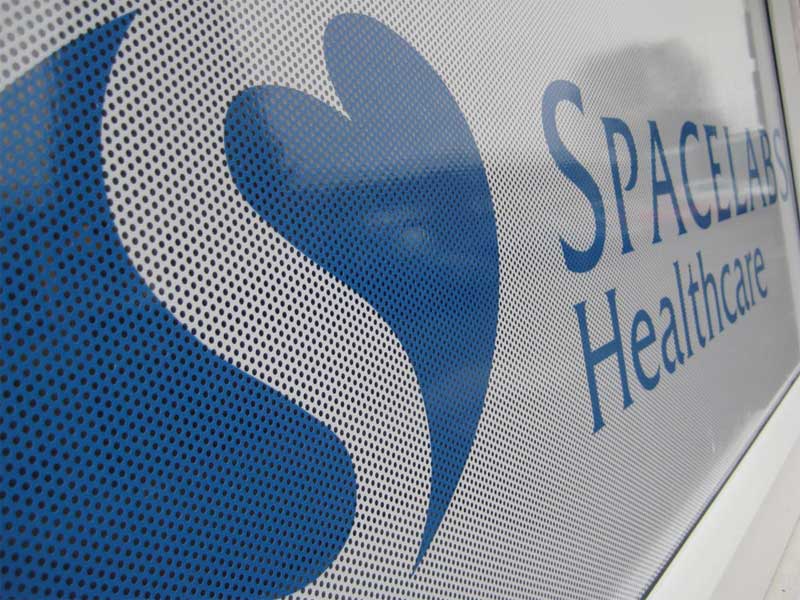
Building wraps
Digitally printed building wrap graphics have been significant in Europe for the last few years and are just starting to show up in North America, mainly for temporary structures at trade shows and other events. The challenge now is to increase the role of these graphics in an architectural context by ensuring greater longevity, which can mean using different materials.
Vinyl for exterior use has certainly seen new advances, including multiple layers and translucent effects, but more durable embedded and sublimated graphics have been more successful at crossing over from trade shows and events into building wraps and façades. Laminates and powdercoated graphics, as mentioned, are well-entrenched in the sign industry.
At the same time, architects are growing more comfortable with specifying digitally printed graphics for large-scale building projects. Compared to commodified vinyl graphics, there is enormous potential for sign fabricators with high-level preparation and installation skills to improve durability and overcome building owners’ concerns about product failure.
One reason this distrust of durability has been an issue is a tendency for multi-year material warranties to be easily voided by certain conditions.
“There are challenges in the preparation of substrates, which often fails,” says Russ Roberts, project director for Creo Industrial Arts, which custom-fabricates architectural signage. “We want to experiment in direct- to-substrate printing and avoid delamination issues. We have had good success with aluminum, for example, and we like how digital powdercoating holds up.”