The measurable point of reference is colorimetric neutral grey balance, which proves no unwanted colour cast is added to the file. Figure 1 illustrates what major print buyers have to deal with when purchasing inkjet-printed graphics after not supplying a hard-proof guide; the leftmost image is accurate to the file, indicated by the neutral grey bar, while the other four images are typical results from non-G7 print shops. The colours in these images may still look good in isolation, with no comparative hard proof, but if the client were selling golf sweaters, then these prints would more than likely be rejected for not representing the products realistically.
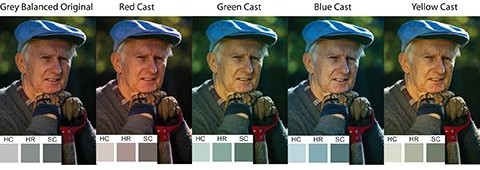
Figure 1: Notice the sweaters. They match the G7 grey balance colour wedge. Grey balance is objective.
G7 provides a solid, indisputable point of reference for file reproduction. This does not mean customers will never again want to adjust colours, but there is now a high likelihood they will accept the logic of G7’s accurate results. They should be happier and more loyal when they can trust the results.
Another way to think of G7 is as ‘process control,’ given it provides base calibration before ICC profiles are applied.
“When we talk about colour management, we tend to talk about instruments, neutral balance and colour difference values,” says Christopher Brown, engineering manager for wide-format printer vendor Mutoh America, “yet when colour management fails, we tend to blame the hardware, software or operator. While software, instruments and well-trained operators are all important aspects of the workflow, colour management must be built on a solid foundation of process control to be effective.”
This distinction is important, as one common misconception suggests ICC provides grey balance and, therefore, G7 adds no value to calibration so long as ICC profiles are used.
“In most cases for inkjet applications, G7 calibration can simply replace conventional linearization, avoiding the need to add another step to the colour workflow,” Brown explains. “Rather than linearizing the printer in the conventional way, which has the effect of calibrating the printer only to itself, G7 calibrates the printer to a set of system-independent aims derived from the native white and black points unique to the printer, ink and media. The number of patches necessary to calibrate the printer need be no more than the typical number used for linearization. It requires no more time nor expertise and the resulting curves can be applied in the same way as conventional linearization curves.”
Fostering calibration
G7 is solving problems in inkjet print production that other printing technologies have not addressed.
The primary market advantage of digital inkjet printers is they can efficiently produce short runs of graphics on a broad variety of substrates, using inks with non-standard colourants. This advantage, however, can also be a disadvantage.
Most of the time, digital inkjet printing can mix light cyan, light magenta, light key/black and even orange and green inks with standard CMYK colourants to achieve the targeted image result. With so many non-standard elements, however, colour management is very important in guiding such results or the graphics will be a mess. Fortunately, once a neutral grey aim point is specified, it is possible to mix all of the colours to achieve base calibration.
When a client sends an image to be inkjet-printed, he/she may have spent many hours correcting that image to exactly the colours he/she needs simulated in the print. So, if the printer adds its own colour cast to the image, the client will not be happy. In the past, sign shops offered excuses like, “We can’t make it any better because of the substrate,” or, “We can’t match the image because we use six colours of ink, not four.”
By starting with G7 calibration prior to colour profiling, on the other hand, it becomes possible to establish a common baseline for grey balance and tonality and even ensure two or more printers produce very similar results.