Wide-format Graphics: The G7 advantage for sign shops
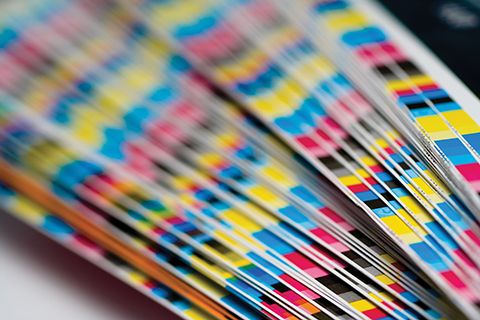
By Mike Ruff
In recent years, an increasing number of wide- and grant-format inkjet printing professionals have recognized the value of the G7 method for process colour imaging and have committed to getting their shops qualified as G7 master printers. They understand the advantages of calibrating their production department’s cyan, magenta, yellow and key/black (CMYK) imaging devices to ensure a visual match, with colour accuracy to each graphic file on the first print.
The primary productivity killer in many inkjet graphic production facilities is the need to make colour adjustments on the press. With G7, however, sign shops can show clients they are ‘in balance’ on the press and can print to a known arrival point with confidence, eliminating most subjective colour tweaking.
“Prior to G7, we were spending at least 30 extra minutes on a job where the customer wanted us to hit their colours,” says Mike Quigley, vice-president (VP) of Sign-Age, which produces grant-format inkjet graphics. “Reprinting to a previous graphic was even worse. We handle a lot of fleet graphics, for example, and customers frequently come to us after a vehicular accident with a request to replace only one section of their wrap. In the past, it was not unusual for us to spend three to four hours trying to get a colour match. Now, using G7 tools, we spend less than 15 minutes.”
It is easy to see how such time savings could add up dramatically and, hence, why every sign and digital graphics shop can benefit by using G7.
Free and independent
Invented by independent colour management consultant Don Hutcheson and published by the International Digital Enterprise Alliance (IDEAlliance), G7 is both (a) a definition of greyscale appearance and (b) the calibration method for adjusting CMYK devices to simulate that definition. It is device-independent, offering the same neutral print density curve (NPDC), grey balance definitions and calibration methodology for any imaging technology, regardless of substrate or colourants.
IDEAlliance, which governs G7 training and use, is a non-profit industry association that guides and publishes specifications and standards for the printing industry. Its primary purpose is to facilitate a level playing field for all stakeholders in developing and advancing best practices. As such, it cannot endorse any particular technology over others.
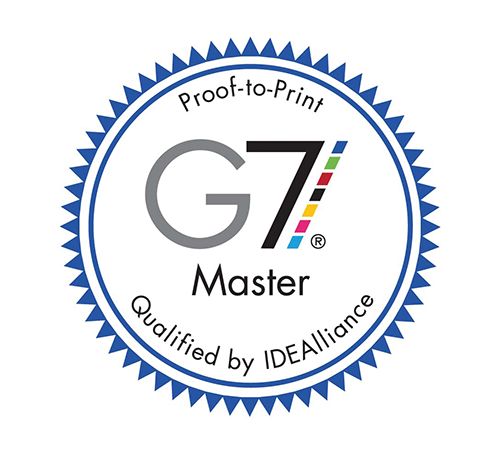
G7 can be implemented and used for free, without buying additional hardware and software. G7 spreadsheets, graphs and other information are available on IDEAlliance’s website (www.idealliance.org).
That said, some software, raster image processors (RIPs) and related equipment have made G7 easier and faster to use. A self-calibrating machine, for example, can be combined with pass/fail software to make the process more efficient. There are many such systems for calibration and control, which IDEAlliance also lists on its website.
Controlling the process
In digital inkjet printing, G7 is mostly used to achieve a neutral grey starting point for colour management, which improves accuracy to targeted print specifications. It helps by calibrating the grey balance of non-standard substrates and inks.
G7 itself is not colour management, nor does it even have to be used with colour management, but in inkjet print production environments, it is most commonly implemented with colour profiles. Indeed, many inkjet devices and RIPs now use G7 to provide a common starting point for the use of International Color Consortium (ICC) profiles.
The trend today is for clients to send a Portable Document Format (PDF) file of their desired graphics, not hard-copy proofs, which has sometimes made it difficult for signmakers to know if their prints are accurate to what their customer wants. G7 provides the methodology (a) to be accurate to the file and (b) to be able to prove that accuracy in a measurable way.