Direct and transfer
To add to the confusion, there are two basic methods for printing with dye sublimation inks onto fabrics: transfer and direct.
The most common method, traditionally, has been to print an image onto transfer paper and then sublimate it onto a coated or uncoated polyester-based textile. In the direct process, on the other hand, the image is printed onto a coated fabric and then sublimated, without the use of transfer paper.
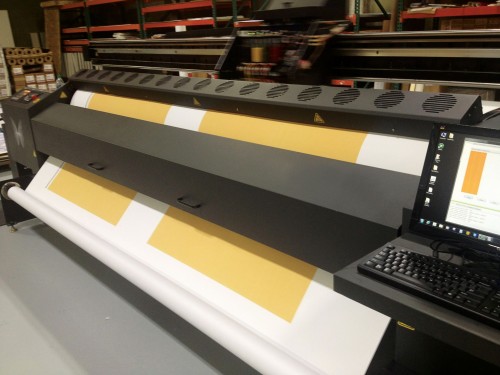
Some presses can print either direct-to-fabric or to transfer paper with water-based dye-sublimation inks.
The advantages of transfer and direct sublimation are still being debated within the industry today. While it is certainly possible to argue about the quality of output from each method, however, the differences between them are much more nuanced than those between sublimation and non-sublimation printing. The choice of which to use will depend on the capabilities of the print or sign shop and the types of printers under consideration.
If a sign shop already has a heat-transfer press, for example, then it would make sense to continue with transfer-based dye sublimation printing capabilities, since stand-alone heat presses generally run at higher speeds than printers.
Other considerations reflect workflow preferences and specific application needs. Some signmakers, for example, prefer to set up a printer profile once for a specific paper and then only change settings on the heat press for different polyester-based fabrics. Others are concerned about the additional expense of the two-step transfer process, as they must buy the transfer paper. The playing field is slightly levelled because direct sublimation requires coated fabrics, which are more expensive than the non-coated fabrics that can be used in transfer sublimation—but the addition of paper is still more expensive at approximately 12 cents per square foot, compared to the additional three cents per square foot for coated instead of uncoated fabric.
If a sign shop has very specific needs for backlit graphics and flags, then it may make the most sense to use direct sublimation, which offers the advantage of a heavier ink load for these applications. With flags, for example, dense ink is typically required to show through both sides. And with backlit graphics, greater ink density means improved colour integrity when light is shining through.
For more precise and detailed graphics, on the other hand, transfer sublimation offers a slight advantage, with little to no bleed when laying ink down on well-profiled transfer paper.
Fortunately, there are some printers on the market today that allow PSPs to choose the best process on a project-by-project basis, supporting both direct and transfer sublimation. Indeed, this flexibility has quickly made these presses among the most commonly installed across Canada and the U.S., at least in the industrial 3-m (9.8-ft) wide category.
In this sense, the industry is balancing the overall market interest in fabric graphics with recognition of the importance of printing versatility.
On-board and in-line
Another advance in dye sublimation printing has been the recent innovation of supporting true heat press sublimation on-board the printer, making the machine an ‘all-in-one’ unit. This is referred to as ‘in-line’ sublimation.
In the past, some textile printers promised on-board sublimation by passing the fabric near a coiled heat source during substrate transport. This was not true dye sublimation, however, as there was no actual contact or pressure and the coils could not generate sufficient heat without the risk of damaging the substrate. The resulting graphics were not water-resistant off the printer and ink could bleed from the print. This necessitated additional steps to fix the final images, including washing and steaming to remove any excess ink that had not been properly sublimated.
Some newer all-in-one printers instead feature a true on-board heat press calender, ensuring the dyes are fully sublimated into the fabrics.