Media selection
While the use of vehicle graphics has become commonplace, concerns remain that relate to both conceptual design and physical durability. If they are to achieve their goals of driving brand awareness and sales, they must withstand the constant tests of high and low temperatures, ultraviolet (UV) radiation, rain, dew, snow, humidity, abrasion and other harsh environmental conditions that could lead to discoloration.
“The horizontal portion of a vehicle is generally of the most concern, as vinyl graphics face the most durability challenges there,” says Jason Yard, marketing manager for pressure-sensitive adhesive film manufacturer Mactac. “The roof and hood are exposed to the elements more directly than the sides of the vehicle and, for this reason, are often the first portions to fail.”
Wrap films are tested in weatherability simulations, which can use special environmental chambers and instruments to accelerate the weathering process and then measure its effects to get a relatively accurate indication of how the films will perform in real-world climate conditions.
“A recent test of one of our products showed higher resistance to UV aging than a comparable product, which began cracking after 6,400 hours,” says Yard. “General performance of overlaminates applied to the printed media was also tested, but little variance was found between the two samples. This highlights why it is important to look at different attributes of materials.”
Some vinyl films are meant specifically for decals and markings, while others are engineered for full wraps. Options include permanent or easily removable adhesives. The degree of curvature of the vehicle will also determine which film is best-suited for the application, as it is important to avoid bubbles along the surface.
“Don’t try to use one film for everything,” says Pate. “Some films are too thick, for example, to wrap the recessed areas on a Mercedes-Benz Sprinter van. You need to mix and match.”
The adhesive’s performance will also depend on the right approach to installation and maintenance. Temperatures between 15 and 35 C (59 and 95 F) will typically allow the adhesive to flow and build a sufficient bond.
Production
Like design, the production of vehicle graphics should also take installation into consideration. Downloading or creating the right printer profile, for example, is key in ensuring the right amount of ink is laid down on the film during printing, so the graphics will be light and dry for wrapping, not too tacky. Similarly, when printing with solvent-based inks, it is important to allow sufficient time for the graphics to outgas properly before installation.
“Too many people only outgas the graphics for 12 hours, then laminate them,” says Pate. “The solvents continue to outgas, but into the adhesive, which will slow down the installation process.”
As for lamination, while a thick layer may work well on box trucks and other relatively flat vehicle surfaces for wraps, thinner is better for cars, given their contours. A thick combination of film and laminate will be slower to wrap, especially on mirrors and bumpers.
Similarly, graphic panels should be sized and printed with the intended vehicle in mind. Pate recommends vertical panels for box trucks and semi-trailers and horizontal panels for vans and sedans.
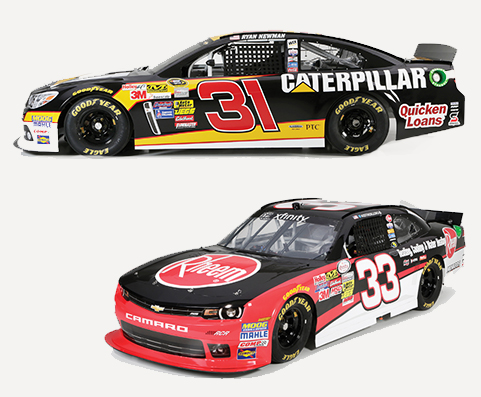
Richard Childress Racing (RCR) prints and installs new wraps for each of its cars before every race.
“At the beginning, everyone used vertical panels for everything because the adhesives were too aggressive to reposition, but they were slow to install because each panel had to be trimmed out quite specifically,” he says. “I now prefer horizontal panels because there is less need to register the graphics to the vehicle. Vertical panels are still better for trucks because it would be more difficult to position long, horizontal panels. And sometimes, depending on the vehicle, a mix of vertical and horizontal panels is best.”
He also recommends printing on 1.5-m (60-in.) wide films, as then a single panel can span the height of a sedan. Some sign shops instead use 1.37-m (54-in.) wide films, which may necessitate printing multiple horizontal panels for the same section of a car, or 1.2-m (48-in.) films, in which case vertical panels may be needed even to wrap a small sedan, spaced out based on breaks for the doors.
“Considering these factors in the design can make perfect registration of the graphics much easier,” says Pate. “The panels should be labelled on the graphic side, rolled up in sequential order and given to the installer with a printed layout indicating which panel goes where. All too often, I have to wrap a whole bus and I have no layout, so I have to physically space out the panels, which is very time-consuming.”