Wide-format Printing: Common colour management mistakes
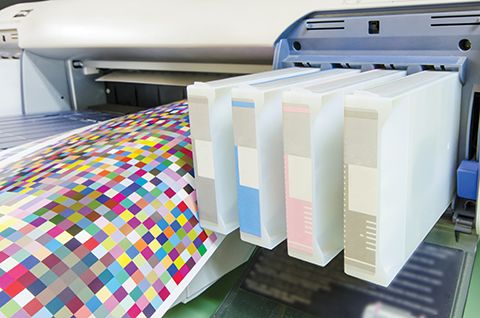
By Mike Ruff
Executing a properly organized colour management workflow can be challenging for sign and wide-format print shops running multiple digital devices and using various ink platforms. As advanced as raster image processors (RIPs) and other software have become, it is essential to achieve process control, not just speed. And while the G7 method for colour process imaging (see Sign Media Canada, April 2015, page 70), published by the International Digital Enterprise Alliance (IDEAlliance), can certainly provide a significant production advantage, it is no silver bullet.
The following are the most common mistakes shops are making with their colour management workflow, based on discussions with dozens of prepress professionals, along with some industry standards and ‘best practices’ to help them get their printing under better control.
1. Trying to correct colour at the press.
In many cases, printing companies tweak colours multiple times to achieve their clients’ given specifications. This approach should not be considered acceptable in a high-volume, profitable production environment. Rather, proper and accurate colour management needs to occur well before a graphic goes to the printer, so as to prevent the need for colour correction.
Unfortunately, it is common for shops to rely on a single media configuration or ‘profile’ for all of their printing. This leads to press operators essentially ‘experimenting’ with colour for every job, rather than knowing what the result will be before the printing process. To maintain this predictability, it is important to evaluate printed results and fine-tune media configurations on
a regular basis.
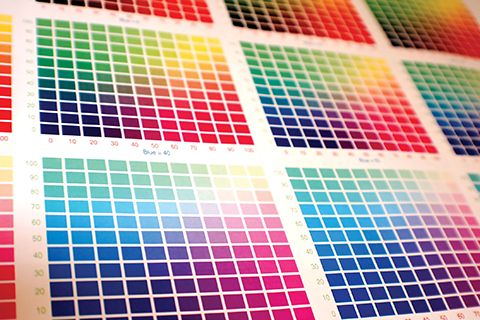
2. Failing to normalize incoming files to be colour-managed.
A recent survey by Xerox found only 20 per cent of digital printing companies preflight their files—leaving the other 80 per cent facing unpredictable print results—and even for those that do, 50 per cent of their incoming files fail. So, they end up complaining about the variability of incoming files.
The obvious solution to this problem is to fix the failed files. This process is referred to as ‘normalization.’
Some print professionals today ‘manually’ preflight and normalize their files with software like Adobe’s Acrobat Pro, but this is slow and can become burdensome as the volume of files increases. Other shops use ‘semi-automated’ software that identifies problems, but can’t always fix them.
Better to use fully automated preflighting software to both find and fix most problems, while flagging the others that cannot be automatically fixed—e.g. missing images—for human intervention. RIPs and other software continue to become more fully automated, but cannot overcome all problems with bad files coming to the press, so it is important
to only send normalized files to the printer.