Wide-format Printing: Common colour management mistakes
3. Altering the underlying characteristics of a device after profiling it.
One common infringement in this regard is applying a correction curve to a profiled device in the hope of improving colour output. This is certainly not the G7 method.
G7 correction curves are applied to the base linearization to grey-balance a device prior to profiling. Alternatively, some RIPs now allow a G7 grey balance adjustment to the linearization after the profiling is complete, which is great for managing a profile and helps avoid reprofiling.
Good profiles do not go bad; they are simply invalidated by changes to underlying system conditions. If a printer operator curves an existing profile, rather than grey-balancing the linearization, he/she is changing all of the colours that have already been matched through the colour management process.
The key is to grey-balance the linearization—not the profile—with G7 correction curves.
4. Viewing colours under poor ambient conditions.
The final approval of a qualified profile is often based on visual assessment, but this will only work if the viewing conditions do not add any colour cast to the image.
To avoid colour cast, it is important to comply with the International Organization for Standardization’s (ISO’s) 3664:2009, Graphic Technology and Photography—Viewing Conditions. Reviewed in 2015, this standard publishes requirements for five conditions:
- Colour quality (including chromaticity, colour temperature and spectral power distribution).
- Light intensity of 2,000 lux for prints and proofs, with tolerance of plus or minus 500 lux.
- Evenness within 60 per cent of 2,000 lux (i.e. 1,200 lux) across the entire viewing surface.
- Neutral and matte ‘surround,’ with luminance reflectance between 10 and 60 per cent.
- Geometry of the light source, image and observer’s eyes, positioned to minimize specular reflectance (i.e. glare).
Another problem can occur with the substrate. Many paper manufacturers today use optical brightening agents (OBAs), but these can actually make white paper appear blue and thus have a negative effect on viewing conditions by causing metamerism (i.e. the ‘apparent’ matching of colours without matching their spectral power distributions). Even this level of colour cast will be unacceptable to clients who require repeatability of their branding.
Colour itself is an effect of light, so colour control relies on well-controlled lighting conditions. Lighting indicator tests are available to assist in achieving such control.
5. Non-calibrated or poorly calibrated monitors.
When addressing ‘soft proofing,’ ISO Draft International Standard (ISO/DIS) 12646:2014, Graphic Technology—Displays for Colour Proofing—Characteristics, explains how to properly calibrate monitors for colour management workflows. Soft proofing really relies on a system comprising the monitor, software, computer configuration and control over the viewing area.
IDEAlliance, for its part, has certified monitor systems in three categories. Full details are available at its website (www.idealliance.org).
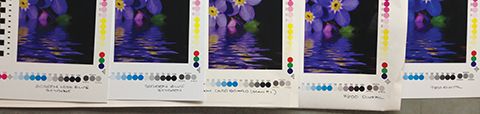
6. Assuming a profile is good forever.
As mentioned, good profiles do not go bad. Nevertheless, process conditions will certainly change over time for a variety of reasons, whether naturally, by accident or on purpose (e.g. when device operators make changes).
A profile is simply a snapshot of a printing environment at a moment in time. When that environment’s underlying conditions change for any reason, then either the system needs to be brought back to its original conditions through relinearization or the device needs to be reprofiled.