Proving compatibility
When a particular substrate has not yet been properly vetted, the most common ‘rule of thumb’ in a tight production environment—where it is often important to keep squeezing jobs through—is simply to make the best guess based on characteristics that are similar to other, compatible media. While this is risky and certainly not ideal, it has become the most common default method for quickly matching media to printers, as it is seen as the only solution in a pinch.
Two fairly similar-looking types of media may both be listed as offering ‘satin’ or ‘semi-gloss’ finishes, yet due to their specific types of coatings and/or the makeup of their base substrates, they can behave quite differently when used in the same actual graphic application. A layer of polyethylene (PE), for example, is frequently used to coat paper, fabrics and other printable media. PE is a strong choice for ink receptivity, but is very susceptible to bubbling or deforming when subjected to heat. So, a substrate coated with PE offers both advantages and disadvantages compared to other products that look very similar. In this sense, many comparable media products are designed for different print purposes.
As such, it is always best to contact each product’s manufacturer and/or distributor and compare all of the information. It is also important to ask how any claims of media compatibility have been determined.
Some manufacturers—and, for that matter, distributors—run their own printers in a lab for quality control and research and development (R&D) purposes. They may also create their own International Color Consortium (ICC) profiles for colour management.
If manufacturers and distributors do not undertake such measures to prove sufficient compatibility between inks, media and printers, then signmakers need to ask themselves if it is worth the risk to take a shortcut and put their own reputation on the line by using unproven products.
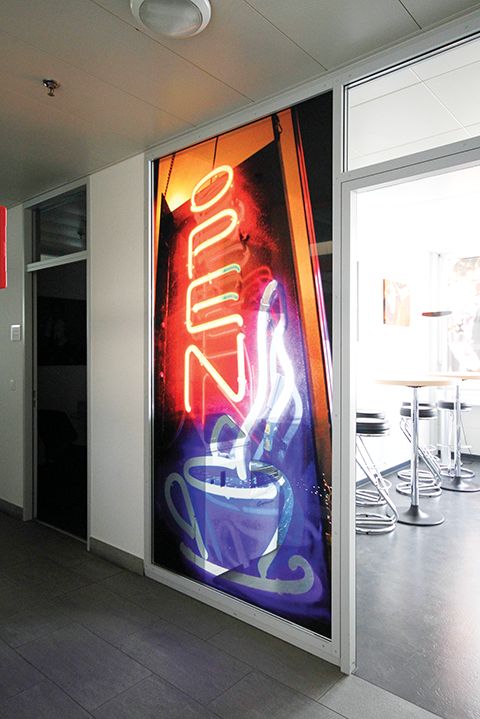
It is important to match the ink density values to the substrate to optimize visual impact without ‘flooding’ the image through oversaturation.
A place for profiles
As mentioned, ICC profiles can be helpful in colour management. Specifically, an ICC profile allows users to pre-set the colour balance and ink level limits for their printer, achieving ‘plug and play’ results for typical, fast-paced ‘on the fly’ digital printing. The difficulty in relying on an ICC profile, however, is it can be seen as a shortcut solution for working with media with minimal graphic performance parameters.
Consider a printable substrate, for example, that does not receive the ink load well. If any ink loads over 70 per cent bled, did not dry properly or exhibited coalescing, then the procedure for creating an ICC profile for that substrate would involve limiting the ink load and maxing out colour at 70 per cent. Linearization would be created with the 70 per cent ink load as the new maximum. Such a process will limit the gamma range by disallowing 30 per cent of the potential ink density that could have been enjoyed with a higher-quality substrate.
Indeed, a higher-quality substrate with a good ink-receptive coating could handle the higher end of ink load saturation and allow for a wider potential gamma range. Simply stated, using higher-quality ‘ingredients’ allows for the production of higher-quality products.
Establishing trust
Last but not least, any checklist for ensuring the right media are matched to the right inkjet printer needs to include ‘trust.’ If all of the other aforementioned steps have been taken, with good-quality supplies used along the way, then the printed output should be predictably reliable.
If any anomalies do show up, they can be addressed in a level-headed manner. Examples include checking how the substrate is fed through the printer, to ensure the feed is taut and there is no buildup of slack. Factors like ambient temperature shifts, humidity, static electricity and power fluctuations can all play a part in throwing off expectations for print performance.
Further, many wide-format printers ‘dance’ back and forth while producing graphics, which can ‘wag’ the output sufficiently to negatively affect the results. To a large degree, addressing such issues is simply a matter of common sense, but the main point is the stronger reliability of higher-quality materials, which allows signmakers to focus on finding the real roots of any problems when variances come up, as they will be confidently producing higher-quality imaged output to begin with.
Bruce Walker is a sales and applications technician for Sihl Digital Imaging, which manufactures papers, films, canvas, banners, fabric transfer paper and other media for digital printing. For more information, contact him via e-mail at wwalker@sihlinc.com.