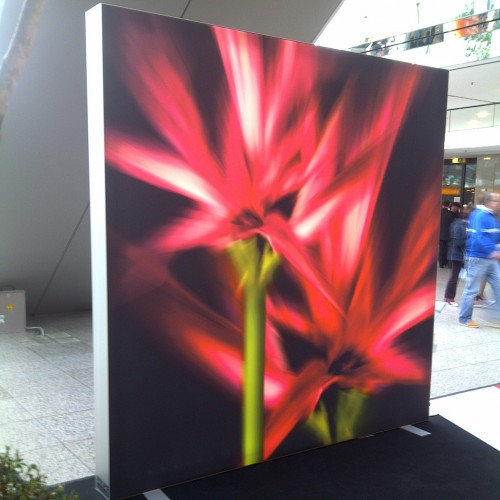
Thanks in part to their non-glare matte finish, dye-sublimated fabric graphics are becoming popular for photographic backdrops. Photo courtesy Comhan Canada
Chemical bond
When dye-sublimation inks or dispersed dyes are printed onto polyester or polymer-coated media, they truly dye the fabrics, as the chemical reaction bonds them to the fibres. A final fixing process is also required, usually involving the application of heat, but the resulting images will never rub or scratch off and there is no change in the feel of the fabric. Pass-through is excellent, making this the preferred method for flag production. Colours are very vibrant and retain sharp details. Upfront costs, however, are high.
Advantages of dye sublimation
The highest-quality method for printing on textiles for signage applications is dye sublimation, which involves printing images either directly onto fabric or indirectly via transfer paper. Under high temperature and pressure, the dye is transformed into a gas to penetrate the fabric, where it solidifies into the fibres.
If done correctly, the dye is permanently bonded to the substrate, so the image is a part of the material and will resist scratching, rubbing off and deterioration.
Dye sublimation inks uses low-energy dispersed dyes, but the inks most commonly referred to as dispersed dyes are high-energy and, when used in direct dye sublimation printers, achieve less than optimal results. They do not sublimate in the same way as low-energy dyes and tend to leave excess ink on the finished print. Truly dispersed dye systems require a wash-and-dry sequence after heating.
As suggested, there are two methods for dye sublimation: direct and transfer.
The first is a one-step process using a digital printer with a built-in heater. This method is sensible for flags and other applications calling for saturation of the fabric to achieve bold colours on two sides.
The second method is a two-step process that first uses a digital printer to produce an image in reverse on coated transfer paper. Then, heat is used to transfer the image from the paper onto the fabric substrate. Compared to direct printing, this results in truer, photorealistic image fidelity and higher resolution.
With the second method, the heat is provided with an external press. The heat must be distributed evenly from left to right. Oil drums tend to be the most efficient tools for this purpose and their size will directly affect production speed. Belt tension control is also important for ensuring image quality and a vacuum will increase ink penetration.
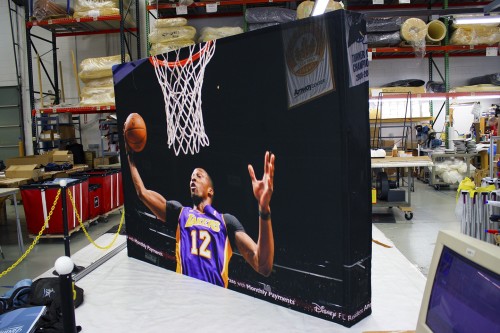
New frames and other display hardware have also fuelled the growing popularity of fabric graphics. Photo courtesy Global Imaging
Making the best decision
If a sign shop needs one printer to produce graphics on both vinyl and fabrics, then a latex inkjet system would be the best option, due to its versatility. For a fabric-only printing system, on the other hand, dye sublimation remains the best bet.
For a low-volume production environment where ease of operation is important, a direct dye sublimation system is a good fit. For maximum flexibility in terms of fabric types and for high-volume production, transfer-based dye sublimation is preferable.
Not every shop is ready, of course, to focus on fabric graphics. Those equipped with a solvent-based inkjet printer could enter the market by starting to offer a limited range of lower-end applications. And in some cases where a signmaker would like to offer fabric graphics, but needs to build up the business first, outsourcing specialized production is a viable alternative.