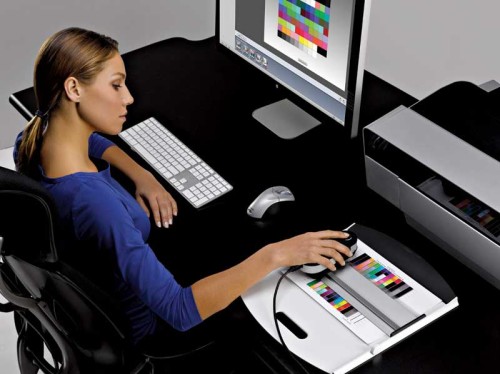
Photos courtesy X-Rite Pantone
By Alfonso A. Hernandez, Jr.
Until the 1950s, there were no real industry standards for the colours of inks used in commercial printing. The Pantone Matching System (PMS) was established because, at the time, each manufacturer of inks followed its own standards and did not share them with their competitors, which became the source of much frustration. If inks were purchased from multiple vendors, the colours would not match. PMS changed this situation with a standardized ink colour book.
Today, by contrast, there are industry standards for colour formulations across not only printing technologies, but also other industries. As trends are monitored across a variety of business segments, more books on colour are published.
Further, colour management—which was a seemingly random process in the 1950s, if it could even be called colour management at the time—has evolved into a completely organized process for the graphic arts industry, from input (e.g. scanning, photography and desktop files) to output (i.e. printed graphics); and from offset to flexographic to toner and inkjet printing; and from simple desktop printers to enormous high-end flatbed presses.
Regardless of how a file is created or produced, customers demand accurate colours matched across a variety of systems, including both monitors and printers. The developments of the past set the stage for the new generation of colour measurement and management expertise that today’s wide-format printing sector has grown to depend on throughout its workflow, from design to production to quality control.
Certainly, achieving great colour output is important for anyone hoping to profit in the sign and display graphics business. When working with wide- to grand-format printing equipment, there are four key considerations for reaching this goal:
- Consistency.
- Calibration.
- Characterization.
- Conversion.
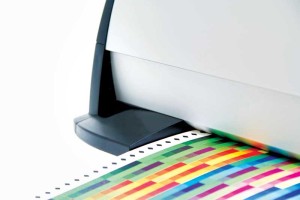
Spectral technology can help manage the complexity of colour-measuring optically brightened substrates.
Consistency
The very first consideration is the condition of the printing device. The printer must already be behaving consistently if colour management is to proceed successfully.
“Getting the device into a known state is the most important process before you do anything else,” says Larry Spevak, president of ColorBurst Systems, which develops raster image processor (RIP) software for inkjet printing.
To this end, proper and consistent maintenance and regular servicing of the equipment will be key.
Calibration
The next step is calibration, which involves adjusting the printer to match a given set of colour values, so as to ensure all printed colours remain consistent throughout the production process.
“Once a consistent condition of the printing device has been established, the next fundamental task that has to be done properly is calibration,” says John Nate, worldwide technical product training manager for Electronics for Imaging’s (EFI’s) Fiery Wide Format colour management software. “I don’t care how well everything else is done; you will not be able to get to your desired results if calibration is done improperly or not frequently enough.”
Nate compares this procedure to baking a cake, where calibration is like setting the proper temperature for the oven.
“If the oven temperature is too low, you will get brownies instead of cake,” he says, “and if it is too high, the cake will burn before it is baked through. This is why calibration has to be done early on. You cannot overcome the limitations later if the calibration is off.”
“In the calibration process, there are three things to consider: printhead height, bi-directional inkjets and the media feed,” says Spevak. “These are relatively easy to calibrate for most devices, but grand-format printers are so fast and are equipped with such a large printhead array, they must be ‘dialled in’ very carefully. Most are set up with a manual or automation calibration routine for this reason.”