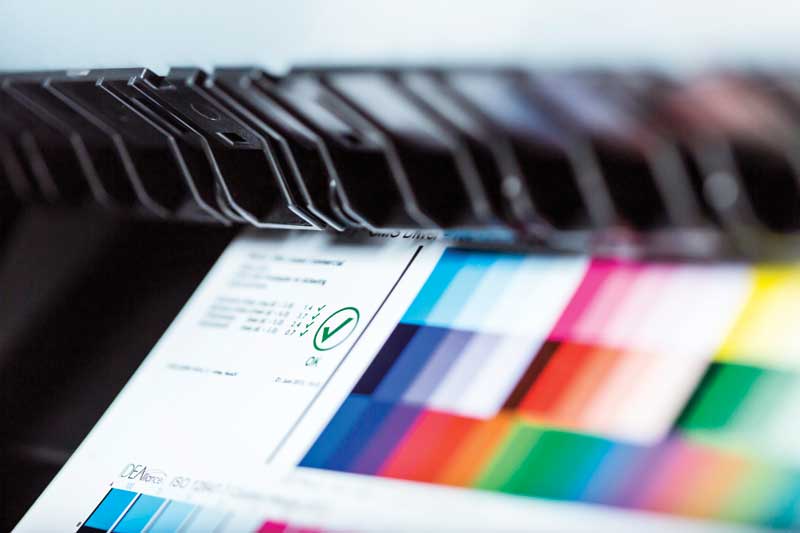
One reason the pre-press process became more decentralized with the advent of wide-format digital graphics is each inkjet printer came with its own RIP software.
Doubling capacity
Decentralized colour management systems can certainly generate somewhat accurate colour, but require a lot of effort to do so. They either use ‘canned’ profiles with a few colour tweaks or develop custom International Color Consortium (ICC) profiles. Colours are measured with a spectral device and various RIPs are used with their dedicated colour engines.
A centralized colour management system, on the other hand, relies on a single RIP to drive all of the digital wide-format printers in the production department. There are no canned profiles. Rather, each profile is created from scratch by the colour management system.
A centralized system can be based on proper calibrations performed to industry standards, such as the General Requirements for Applications in Commercial Offset Lithography (GRACoL). With a quality assurance program in place, regular calibrations and maintenance are performed to ensure consistent results.
In facilities that take the centralized approach, most jobs are completed in the first cycle, perhaps with an occasional second cycle for press approval purposes. As a result, the total labour costs are typically between 10 and 40 per cent of those incurred with most decentralized systems.
Indeed, a print facility freed of performing more cycles per job can typically double its throughput with the same number of staff. It takes less time to get jobs on press and then the press operators can focus on their workloads without the machines being left idle.
Improving profile creation
Among the expenses most print service providers (PSPs) never consider is the investment in time required to create profiles for each of a series of digital inkjet printers.
By way of example, one particular large-volume PSP operates a variety of flatbed and roll-to-roll (RTR) presses, including seven identical RTR models. Using a decentralized, RIP-based colour management system, it took a minimum of three hours to create an ICC profile for each of those seven digital presses, even though they were identical, for a total of 21 hours per substrate. And doing so was necessary not only each time one of the existing printers was replaced, but even each time a single new printhead was installed in one of them.
Today, with a new, centralized system, it only takes about 90 minutes to create a baseline profile on one of the printers, at which point it is automatically shared among all seven identical presses. The company does recalibrate and linearize the performance of the printers to ensure they produce identical results, but this process takes less than half as much time as creating a new profile. Whenever a printer or printhead is replaced, it takes less than 40 minutes per substrate to match the new device to the others. And the results are more accurate than before.
Indeed, the process of colour matching has improved. Whenever the company matches a Pantone colour on one of the printers, the software shares the data with the other six.
The recalibration process is highly valuable. If a colour was tweaked in one of the seven identical printers six months ago, for example, but now one of those presses has drifted, then once the company recalibrates that machine, any previous colours in its library are also adjusted to perform just as before. In the past, on the other hand, colours would drift so far from their targets and linearization was so far off the mark, the only answer in most cases was to spend time building new profiles.
With the previous system, about 15 per cent of files to be processed required colour corrections. Usually, these corrections took three to five cycles. On average, it would take two to four hours before actual print production could start. The machines generally sat idle for one to three hours.
Now, thanks to centralized colour management, the company has reduced the need to retouch files by 90 per cent. The few jobs that still require some colour corrections usually only need one to two cycles. The presses rarely stand still.
Beyond the economic advantages of saving time and labour, the company can now print jobs across different machines with greater certainty the colours will match. Jobs requiring multiple printers and substrates—which comprise much of the company’s work—are now easier than before.
There used to be occasions where one printer would need to be isolated to produce an entire job by itself. Now, the company is so much more comfortable with its colour management efforts, it can instead spread one job across all seven identical presses.
Automation is highly beneficial. Since the installation of the centralized system, the company has increased its sales by 100 to 200 per cent, while only increasing staffing by 20 per cent.