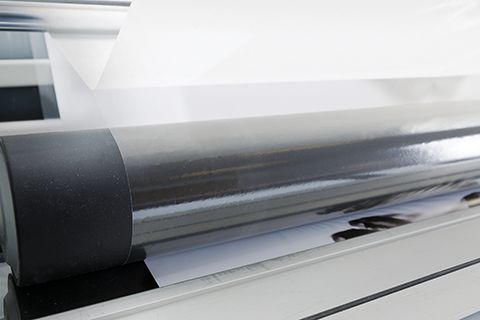
All laminators have different optimal settings for threading an overlaminate through the rolls. Photo courtesy RTape
Speeds and settings
Pressure-sensitive films usually laminate better at slower speeds, e.g. in the range of 0.9 to 1.5 m (3 to 5 ft) per minute. Pressure-sensitive overlaminates require pressure so their adhesive properly flows out and makes complete contact with the print surface. Insufficient pressure can result in ‘silvering’ and the formation of air bubbles. Conversely, excessive pressure can cause wrinkling and curling of the print.
Overlaminates generally require 207 to 345 kPa (30 to 50 psi) of pressure. If air bubbles appear, the nip pressure should be increased, the lamination speed should be slowed down and, if worse comes to worse, a little heat should be added. Thicker overlaminates, including 0.13 to 0.38-mm (5 to 15-mil) thick polycarbonate films, typically require higher pressure settings. One option is to use a ‘sled’—i.e. a 3-mm (0.12-in.) thick polycarbonate or acrylic sheet—underneath the print to help increase and even out the pressure across the laminator’s web.
There are opposing arguments with regard to the application of heat when laminating a pressure-sensitive film. Some people say it allows the overlaminate’s adhesive to flow out better, in turn achieving a stronger bond and preventing silvering. Others point out heat can cause the overlaminate to stretch, such that after it cools, it contracts and can thus delaminate from the print. As heat can also cause other problems, including waviness, tunnelling and wrinkles, it is best not to use it except when absolutely necessary.
Rolling laminated prints
Laminated prints should be stored and shipped flat whenever possible, especially those using polyester-based overlaminates. If graphics must be rolled, a flexible overlaminate like vinyl is preferable and the printed image should be on the outward-facing side of the roll.
The print should also not be rolled too tightly or tunnelling could result between the overlaminate and the print. The outside diameter of the rolled film’s core should be no less than 152 mm (6 in.) for a vinyl overlaminate on a vinyl print and no less than 305 mm (12 in.) for graphics protected with a 0.13 to 0.38-mm (5 to 15-mil) vinyl or polycarbonate overlaminate. In other words, the thicker the overlaminate, the larger the core diameter should be.
Cleaning graphics
Finally, customers will need to be taught how to properly care for their newly delivered graphics. Laminated prints should be washed with sponge or soft rag—as hard bristle brushes can scratch the surface, especially with 0.08-mm (3-mil) thick polyvinyl chloride (PVC) films—and a mild, non-abrasive cleaner that is neither too acidic nor too alkaline and does not contain strong solvents. After cleaning, the graphics should be dried using a soft, clean cloth towel, avoiding paper towels that could also scratch the overlaminate.
Jim Hingst is a 42-year veteran of the graphic arts field who retired from application tape and premask manufacturer RTape earlier this year. For more information, visit his blog at www.hingstssignpost.blogspot.ca.