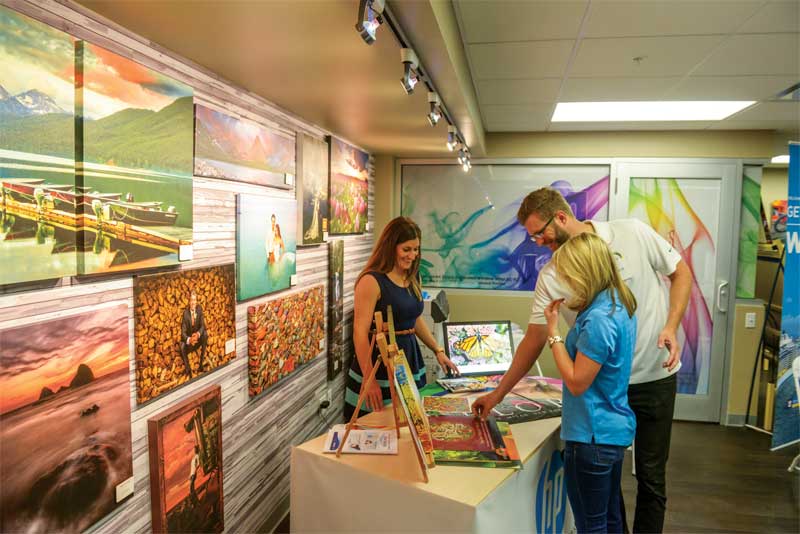
As with the inks used in wide-format printing, the chemical exposure relating to textiles is an important concern for those using the materials in finished applications, particularly indoors.
Photo courtesy LexJet
Claim verification
If a product is advertised or sold based on a specific performance feature, then it is important to back up these statements with meaningful, standardized test results. Sign shop owners and other professionals are increasingly savvy and suspicious of promotional rhetoric. A test result is more powerful than empty claims of a textile’s stain resistance or reflectivity.
The same is true of comparisons to a competitor’s product. All companies can say their products are the best, but only standardized test results can provide quantifiable evidence.
Next steps
Today, with many new textiles continuing to be introduced for the digital wide-format printing sector, standardized testing plays an important role in overall quality control and in further research and development (R&D). If signmakers get involved with the relevant SDOs, then they can help ensure their own interests are represented as new methods are developed. By being part of the process, they will also get a ‘sneak peek’ at the types of standards their customers may demand they comply with in the near future.
This is the time to (a) take advantage of the resources offered by SDOs and other players in the industry and (b) propose ideas and work with others to turn them into reality. By working together, the industry can increase the chances of developing better methods than any one party could accomplish on its own.
Diana Wyman is technical director for the American Association of Textile Chemists and Colorists (AATCC). This article is based on a seminar she presented in October at the Specialty Graphic Imaging Association’s (SGIA’s) 2017 Expo in New Orleans, La. For more information, visit www.aatcc.org and www.sgia.org.
standardized testing matters